Introduction
Part 1 of this blog (HE, March 2018, pp 101-108) had discussed a methodology developed by the authors of this series to benchmark a refinery’s fuels blending system. This methodology produces two indices, namely, automation effectiveness and operational efficiency, to assess both the refinery’s infrastructure and operating practices. This methodology creates a rank to compare with other refinery’s blending systems. It also gives qualitative and quantitative criteria for the required investment to upgrade their fuel blending system to bring it to par with other refineries in the world and to capture the lost benefits due to the sub-optimum blending system at the refinery.
Part two of the series discusses how this methodology is executed by presenting the phased process in a case study for a 300KB/day refinery in south Texas, USA. The services of the authors of this blog were retained by the refinery to assess the current state of their fuel blending and recommend the steps to revamp their blending system, if found feasible both technically and economically.
Case study objectives
The refinery management had the following objectives of the project.
- What is the state of the fuel blending system in the refinery?
- Is it at par with other refineries?
- How to minimize the giveaway and reblends of fuels?
- Can we estimate how many benefits we are losing in quality giveaways?
- Are our recipes optimized?
- Are we using the latest technology?
- What will it take in terms of the investments to revamp and/or upgrade the blending system?
- What is the latest online analyzer technology?
- What will it take to incorporate into the refinery’s blending system?
- What do we need to train our staff in terms of narrowing the capability gaps?
- What will be required for change management?
Figure 1. Blending Automation Islands
The refinery’s expectations were in line with wanting to assess their fuel blending system. They needed to look at the blending system from two perspectives, namely, technology and management. Hence, they decided to retain the services of the authors of this paper for the technology part and another management consulting firm to look at the management of capability gaps and change management. This blog will only discuss the work contributed by the authors of this paper [1,2].
The study project was spread over 6 months with a bi-weekly review meeting to discuss various aspects of the project. The authors of this blog and other management consultants divided the project into the following three areas of focus. We will discuss each of these areas and their sub-areas in detail in this paper and finally present our recommendations for this case study.
- Infrastructure and Technology
- Capabilities and Change Management
- Recommendation for the System improvement
- Assessment of existing blending Infrastructure – The first step of this study was to review the existing infrastructure for the blending system, compare it with most state-of-the-art installations, and generate a comparative status matrix. This step will generate an “Automation Effective” index as discussed in part-I of this paper. The methodology adopted for this step is discussed in the following paragraphs.
- Preview of Blending Automation Modules – We had discussed the typical ten automation modules for a modern fuel blending system and shown again here in Figure-1 for the purpose completeness. It is not necessary that any refinery would have all the required ten modules for the blending, certainly, the refinery in this study did not have. The first step was to assign a relative degree of importance for each of these automation modules.
- Assessment of existing blending Infrastructure – The first step of this study was to review the existing infrastructure for the blending system, compare it with most state-of-the-art installations, and generate a comparative status matrix. This step will generate an “Automation Effective” index as discussed in part-I of this paper. The methodology adopted for this step is discussed in the following paragraphs.


Table 1. Relative Ranking of Automation Areas
The authors of this blog series adopt the method to assign the relative merits of these modules based on rankings assigned to each area considering four affecting factors, namely, manpower, automation, HSE (Health, Safety and Environment), and Benefits. Table-1 shows the relative ranking we assigned to each of the above influencing factors to each of the automation modules. Please note that these rankings are not absolute in nature and may be subjective. However, we believe that the overall rankings will be within +-10%.
We arrived at the weighted ranking of the tank farm, for example, by multiplying the relative weights of the four factors and their assigned ranks (1-10) based on our experience in the industry as shown below:
Tank Farm Weighted Rank 4.90 =.15*3 + .35*3 + .20*8 + .30*6
The relative rounded weighted factor of 10 was arrived at as 9.54=4.90*100/51.35
- Generation of existing Infrastructure status matrix – Next step in this methodology is to enlist all sub-components of each of the automation islands shown in the table and determine their exiting state for this refinery. We have illustrated this process by selecting tank farm and have detailed all sub-components and their relative ranks and their actual status. This is shown in table-2. We determined the state of the component with the following automation considerations.
- The number of component tanks should be twice the number of blend components to facilitate automation of tanks closing while blending to avoid the change of component qualities during blending.
- All required signals (especially density) should be available in the automation gauging system, otherwise, it will depend on the lab analysis to calculate the mass inventory of the tanks.
Table 2. Status Ranking of Existing Tank Farm Infrastructure
- All tanks’ inlet/outlet valves should be remote automated to facilitate blend-line up and switching component tanks while blending.
We analyzed other blending automation islands in the same manner as tank farms and calculated their individual automation effectiveness as shown in column “weighted Ranking” in Table-2. Table-1 shows that the overall Automation Effectiveness Index for the blending infrastructure is 51.35 which is a summation of all automation effectiveness indices for all automation blending.
- Assessment of Existing Blending Technology – Next, we will examine how efficiently the blending infrastructure is used in the refinery for the execution of blends to generate another index, namely, the Operational Efficiency Index. This index was calculated based on the following criterion of blending system performance:
- Minimum the blending quality giveaway
- Minimalize the reblends
- Optimize the usage of blend components
- Minimize the inventory of the tanks
- Use of non-linear blend models and optimizers
- Feedback of final blend analysis to update blending models’ error to minimize the blend quality prediction error
- Efficient planning and scheduling of blends
These steps were detailed in Part 1 of this series and hence will not be discussed here. However, we will discuss the process of re-optimization of historical blends to estimate the Operational Efficiency Index. We used SLP (successive Linear programming) and non-linear blend models with custom-developed Excel as the front end by the authors. The computational steps were as follows:
- Collect the historical blend data for 3 months (minimum) based on our requirement
- Develop interface with Excel and our optimizer system to populate the database
- Predict the quality of each blend using a fixed recipe as used in each blend and recalculate model error or bias using the back-casting method.
- Optimize each blend again using the model bias to estimate the lost benefits due to quality giveaway and sub-optimal usage of the blend components
Table-3 shows all factors considered for the blending operational efficiency and we followed the same method to assign a ranking to each of the items in Table-3 and analyze their existing state as a percentage of the desired state.


Table 3. Blending Operational Efficiency Index Estimation
We have shown the procedure to estimate Automation Effective Index and Operational efficiency index in the above paragraphs. Part-I of this blog series discussed that these two indices can be used to estimate budgetary requirements to upgrade the refinery’s fuel blending system and estimate additional benefits from improved blending operational efficiency.
Advantages of the benchmarking methodology
Another important advantage of this benchmarking methodology is that it can be used to compare the fuels blending system across all refineries of the same corporation or with other refineries in the world. Figure-2 shows a representative comparison of these two indices across worldwide refineries.
Figure-2 shows that a lower automation effectiveness index represents higher capital investment whereas a higher efficiency index means a higher return on investment. The refineries can track their fuel blending system state by re-estimating the indices either by themselves or with the help of the authors of this blog.


Figure 2. Relative comparison of Indices across refineries
The result of this master plan study and estimation of the two indices was to recommend a project plan to upgrade the refinery’s fuel blending system by implementing the following systems.
- Multi-period/multi-blend offline blend optimizer
- Tank farm management system
- Tanks quality tracking system [3]
- Online multiplexed sampling system (NIR)
- Revamp field equipment and instrumentation
- Online Blend Control and Optimization System
- Other peripheral systems as enlisted in Table-3
We have shown in Figure-3 that the phased project implementation plan will outweigh ROI versus project cost over elapsed time due to high and immediate return from the implementation of offline blend optimizer. The offline blend optimizer does not require any capital investment and is based only on software acquisition and its implementation.
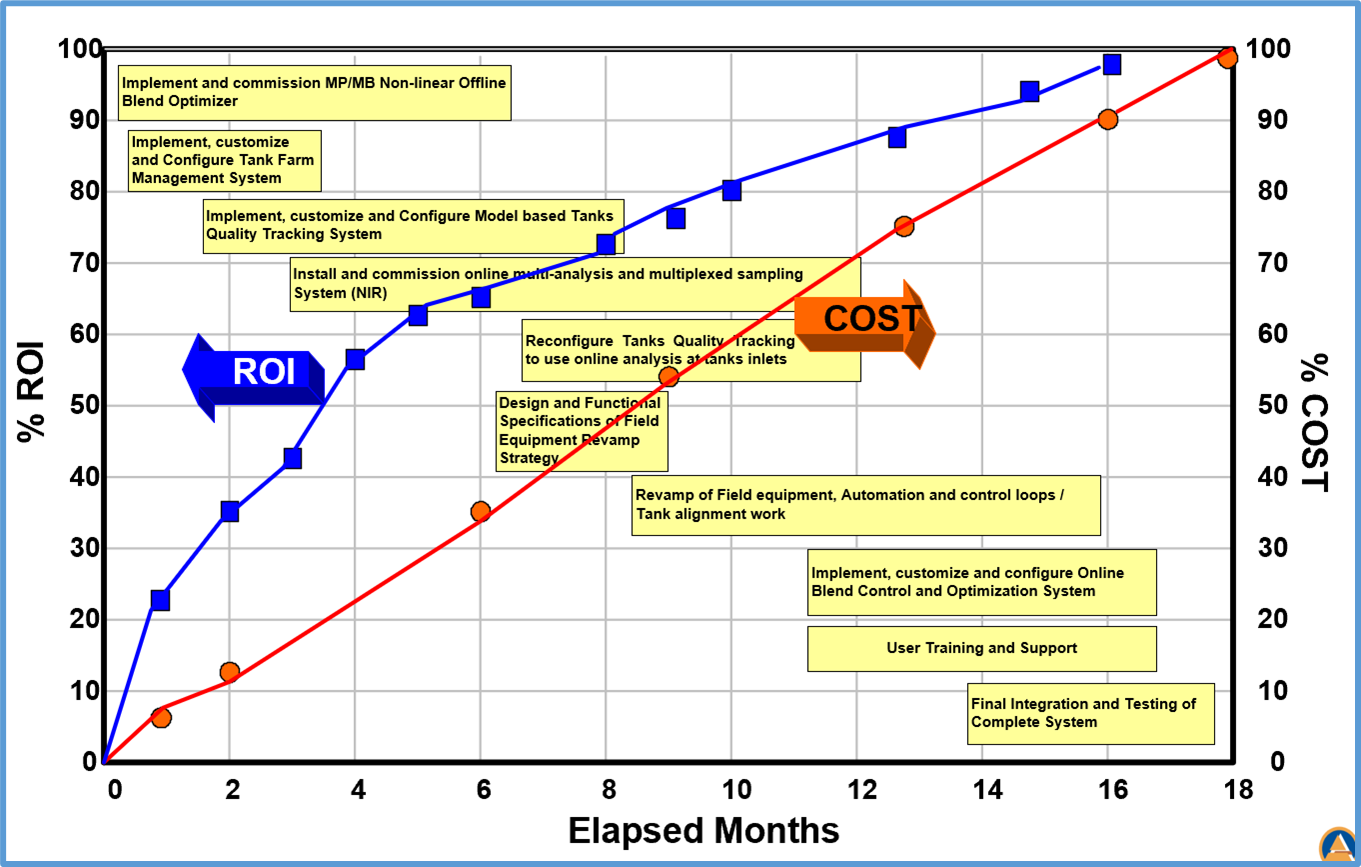
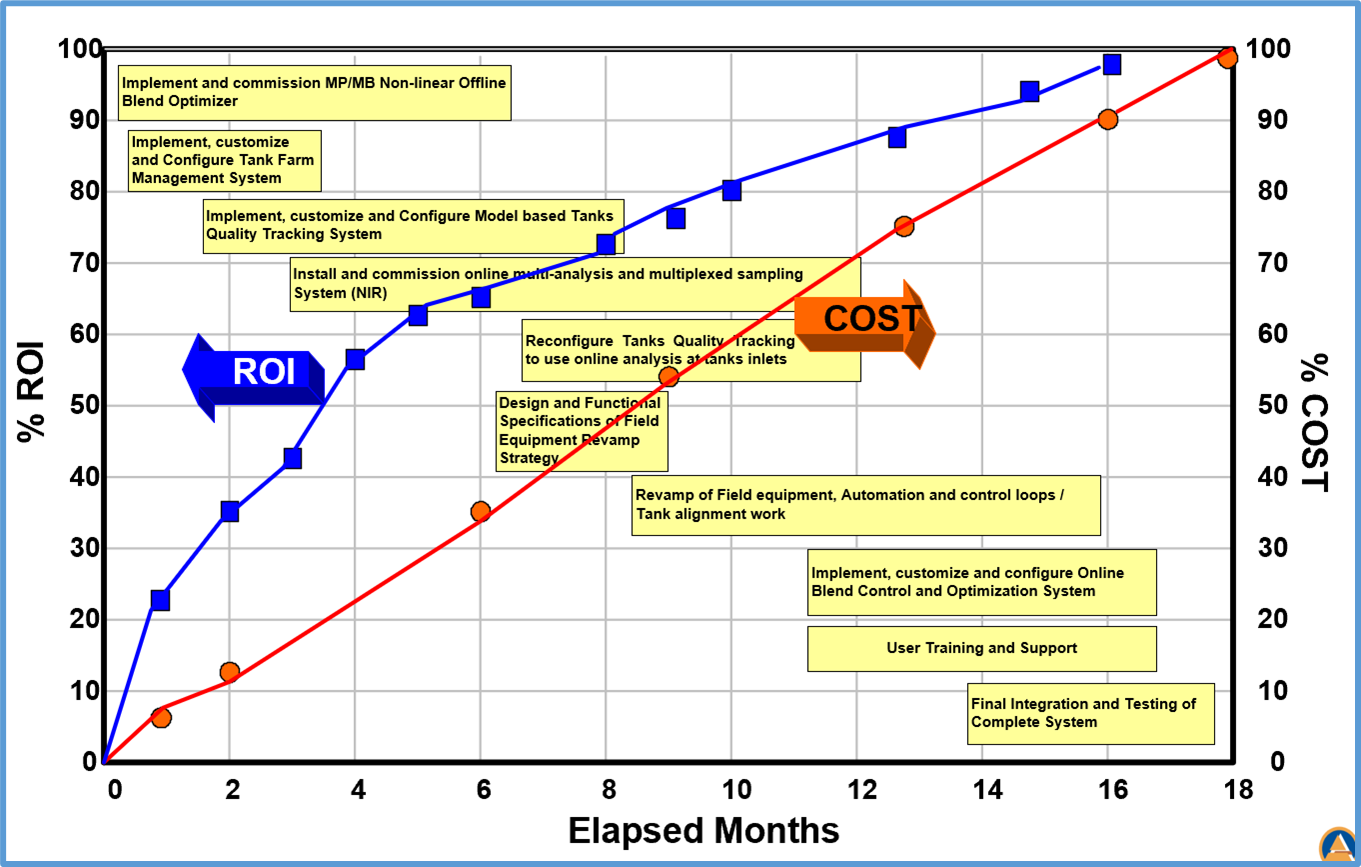
Figure 3. Recommended phased Project Implementation Plan
Conclusions
In this blog series Part I and II, we discussed the Methodology to benchmark refinery’s fuels blending system in terms of two indices, namely, the Automation effectiveness index, and Operational efficiency index. The first index assesses the state of the refinery’s blending infrastructure and the second index assess how efficiently the blends are executed Part 2 of this series discussed in detail the calculations of both indices using weighted ranks to automation islands and their sub-systems in detail The ranks were given using the experiences of authors of this paper and may have some subjective components to it but they are estimated to be within +-10% margin of errors.
These indices can be used to compare the fuels blending system among corporate refineries or with other refineries in the world Recommended project plan used phased implementation to realize ROI quickly and more than the cost incurred along the timeline.
References
- Agrawal, S.S., M. J. Naughton, “Advanced Gasoline Blending-II”, Oil & Gas Journal, Vol-103.7, pp 52-57, February 21, 2005
- Agrawal, S.S., “Advanced Gasoline Blending-I”, Co-author: M. J. Naughton, Oil & Gas Journal, Vol-103.7, pp 50-53, February 14, 2005
- Agrawal, S.S., Leong K.M., Wee L.H., ECT James CTJ, “Implementation and Benefits of Online Tanks Quality Tracking System in a Singapore Refinery”, Hydrocarbon Asia, Vol-15, No-1, pp 36-47, January/February 2005
About the authors
Suresh Agrawal is the founder and CEO of Offsite Management Systems LLC (OMS), Houston, Texas, USA. He graduated from the Indian Institute of Technology, Mumbai, India with a Bachelor of Chemical Engineering. He then obtained a Master’s and a PH.D. degree in Chemical Engineering from Illinois Institute of Technology, Chicago, USA.
Dr. Agrawal has 30+ years of experience at senior technical/management positions with international companies and he has successfully managed many advanced refinery process control projects in numerous countries. Dr. Agrawal is a registered professional engineer in the state of Illinois, USA, and is a member of the American Institute of Chemical Engineers and Instrumentation Society of America. He has published and presented 20+ papers in international publications and conferences in the areas of advanced process control. He has also acted as a consultant to many refining and process industries worldwide and delivers training seminars in the areas of his expertise.
Meena Agrawal is the co-founder and President of Offsite Management Systems LLC (OMS), Houston, Texas, USA. Meena is responsible for project management and execution as well as clients’ relations and business development. She graduated from Roosevelt University with a Bachelor’s degree in Chemistry and an Associate’s degree in Computer Science from Morris County College, New Jersey.
Mrs. Agrawal has 20+ years of experience as technical lead/project management positions with major international companies such as Phillips 66, Exxon-Mobil, Apache Corp and handled projects for windows 7 migration, domain and system separation for ConocoPhillips and Phillips 66, Upstream (EU) application suite for supply and nomination, upstream gas/oil wells test and production data management, etc.
#RefineryBlendingSystem #BlendingAutomationModules #AutomationEffectivenessIndex #OperationalEfficiencyIndex #Non-LinearBlendModels #SlpBlendModel #Multi-BlendOfflineOptimizer #TankFarmManagementSystem #OnlineBlendControl #TanksQualityTrackingSystem #OnlineMultiplexedSamplingSystem #RevampFieldEquipment
1 2 3 4 5 100%
1 2 3 4 5 0%
1 2 3 4 5 0%
1 2 3 4 5 0%
1 2 3 4 5 0%