Introduction
The activities of a typical refinery or any processing plant can be categorized into a number of major broad areas. The viability of a plant depends upon how these areas are managed, integrated, and structured to meet operational requirements, market demand, fluctuating source and quality of raw materials, and many other factors which are sometimes unpredictable and may be uncontrollable.
This paper discusses the automation modules required for integrated Advanced Control and Optimization Systems for a Refinery.
Table -1 below gives the refinery activity and related integrated computer control and/or optimization system for the activity.
Refinery Activity
|
Integrated System
|
This blog discusses the scope and benefits of the following three integrated computer control and optimization systems for the activities given in the above table.
- Crude Blending Control and Optimization
- Product Blending Control and Optimization
- Oil Movement & Storage system
Since the details of each of the above systems are discussed separately elsewhere, this blog presents only an overview of these systems to indicate their complexity and importance for an automated refinery.
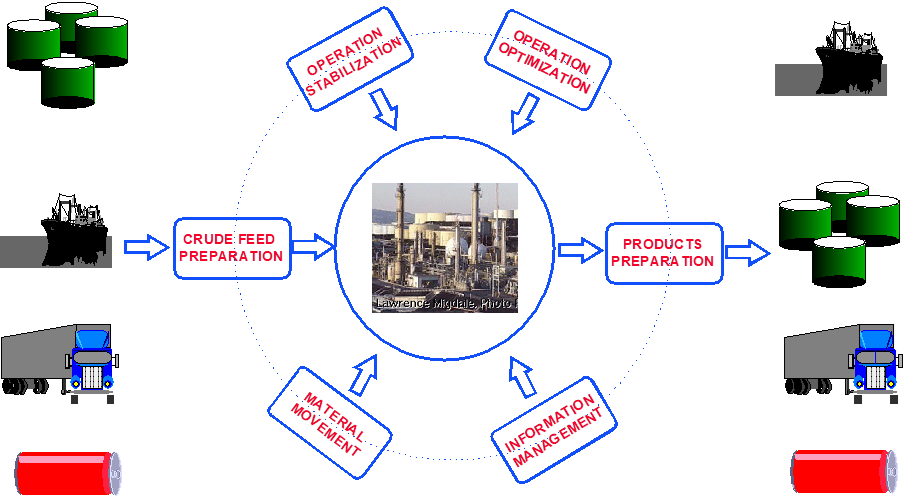
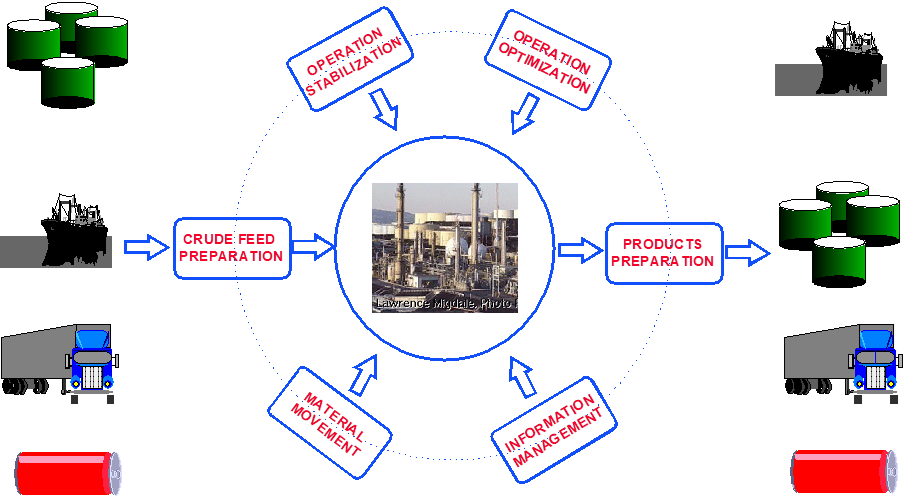
Figure 1. Major Activities in a Typical Refinery
Crude blending
A typical refinery gets its crude supply from various sources that vary greatly in properties such as density, sulfur content, and volatility, and consequently, vary the feed quality to the crude unit. Ideally, the crude distillation unit in the refinery needs to be optimized online for yield and cut quality for product blending and other product slates for every crude feed, but may cause variation in the tower operational parameters and may not be desirable. Alternatively, crudes from various sources may be blended upstream to produce a uniform feed to the crude unit. The implementation of crude blending control and its integration with other sub-systems can achieve the following objectives.
- To minimize the dependency on the source for the crude feed properties and thus stabilize and optimize the operation of the crude unit.
- To maximize the side-stream yields and optimize targeted side stream qualities for product blending.
- To improve crude oil inventory for just-in-time manufacturing.
- To reduce demurrage cost by better planning and scheduling crude unloading operations.
The integrated crude blending system
The benefits of crude blending by itself can not be realized unless it is integrated with other sub-systems for optimization, operational stability, and just-in-time manufacturing. These sub-systems can be categorized into two areas, namely, modules for crude quality control integration and modules for product quality control integration.
Crude quality control sub-systems
The crude quality control sub-systems and their roles in integration are as follows:
No. | Crude Quality Control Modules | Purpose |
I. | Marine Planning and Scheduling | To interface with ships’ arrival schedules and plan a strategy for unloading of crude into crude tanks based on the refinery operational targets. |
II. | Movement Task Monitor and Control | To automate the crude unloading operation into crude tanks based on the strategy planned by Module-I. This module is mainly responsible for Oil Movement and Control (OM&S) functions. |
III. | Crude Tank Composition Monitoring Control and Optimize | To compute the composition and properties of each crude tank for current tank contents. This module also computes the optimum crude mix recipe for each tank based on planned crude unloading and short-term refinery run plans for the crude units. |
Product quality control sub-systems
No. | Product Quality Control Sub-System | Purpose |
IV. | Crude Unit Model | To feedback the target crude feed properties to the crude quality control module-III to optimize the crude mix recipe for the crude unit. This module also set the target for the operations of the crude unit distillation unit for module II described below. This module closes the loop and integrates both product quality control and crude quality control modules. |
V. | Crude UnitLP Optimizer | To optimize the operation of crude units based on the target side-stream qualities and draw-off rate. This module uses model-based control using the LP algorithm. |
VI. | Product Blending LP Optimizer | To optimize the recipe for product blending based on product specs, component qualities, availability, and other constraints. This module uses feedback from an online blend header analyzer to adjust the setpoints of component flow rates. Tank quality integration adjusts online the target specs for the product tank during blending. |
Figure-2 shows a graphical representation of crude quality control and product quality control sub-systems for an integrated crude blending, scheduling, and optimizing system.
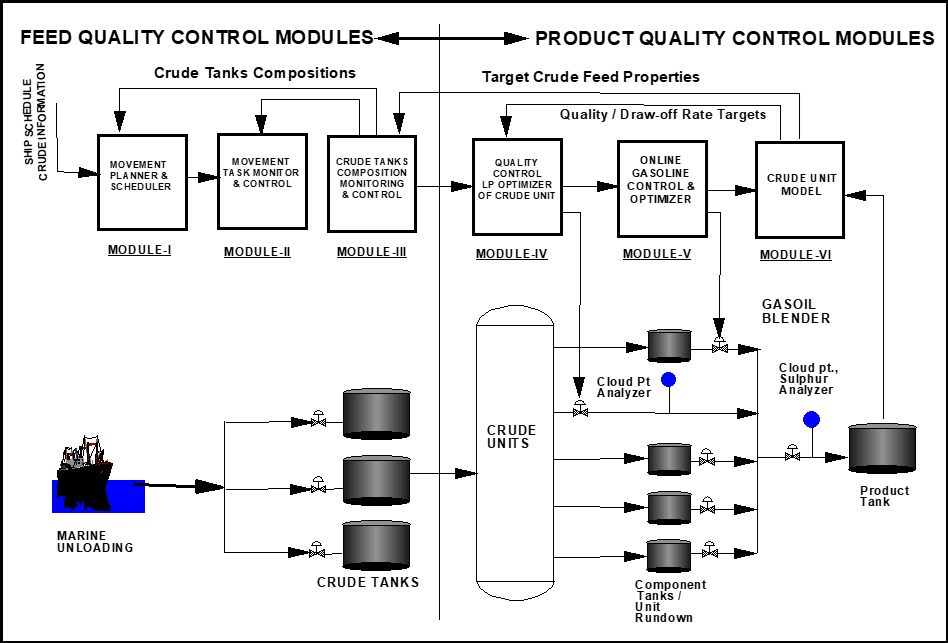
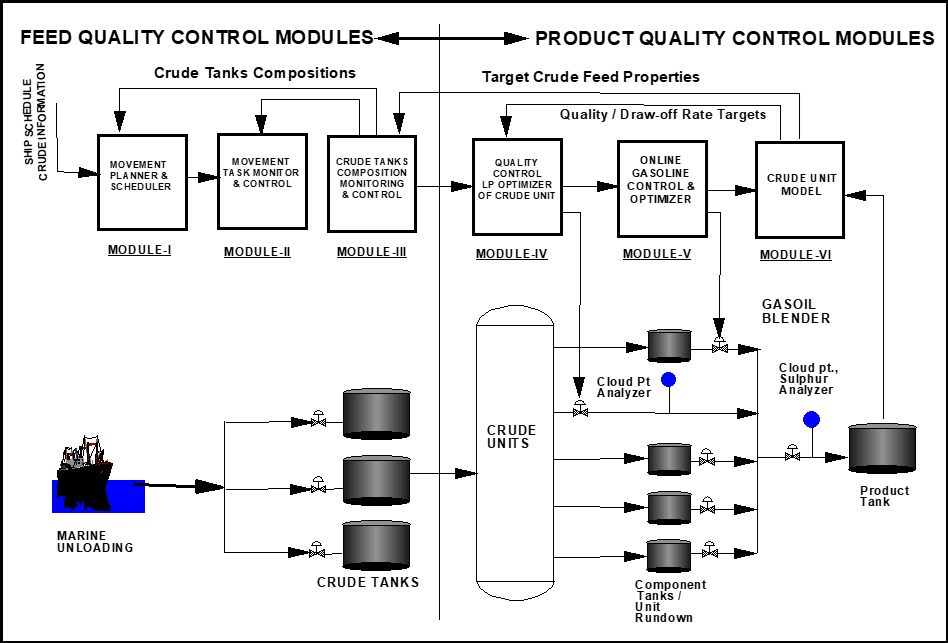
Figure 2. Integrated Crude Blending Control System
Feasibility of crude blending in a refinery
Operational data analysis
- Types of OM&S activities and their relative distributions
- Crude oil types and their receipt volumes
- Schedules of marine unloading
- Schedules of crude types and their feeding to crude units
- Relative percentages of transferring slop (volumes and occurrence frequencies) from other process units.
Operational and physical constraints
- The insufficient number of crude tanks for blending: This may be due to types of crude processed, downstream processing demands, ships’ schedules, etc.
- Lack of free space to install new crude tanks and/or pipelines: This may be a physical limitation despite the economic feasibility of crude blending.
- Segregation of crude types and allocation of specific crude tanks for them: Low sulfurs crude and high sulfur crude will be kept in separate tanks to avoid contamination.
- Recirculations and “tank to tank” transfer activities: Recirculations of feed tanks may limit their use for blending.
- Configurations of “tank to unit” activities in crude oil: This is an operational constraint as it determines the feasibility of blending crude before feeding to the unit. For a typical refinery with two crude units, there are four types of “tank to crude unit” transfer activities and are as follows:
- One tank feeds to one crude unit only.
- One tank feeds to both crude units.
- One tank feeds to both crude units simultaneously and another tank also feeds to one of the crude units.
- Both tanks feed to both units simultaneously.
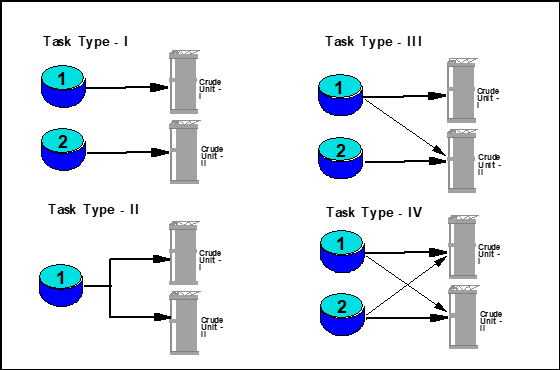
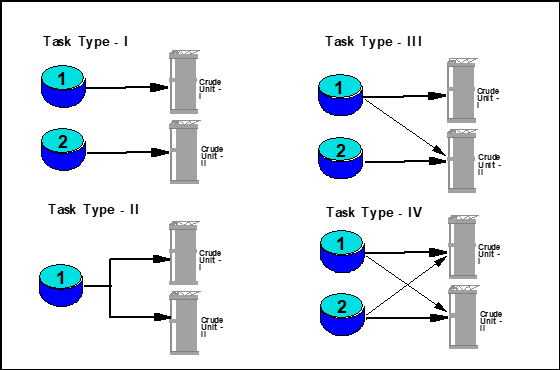
Figure 3. Configuration of tank-to-units Transfer Activities
Configurations of blending schemes
It is clear from the previous section that the configuration of the blending scheme for crude depends greatly on the operational and physical constraints and may defeat the economic advantages. There are three following scenarios for the blending of crude.
- “Ships to tanks” blending
- “Tank to tank” blending for crude feed
- Inline blending from tanks to units
Figure -4 shows various schemes for unloading and blending of crude from ships to tanks. Transfer types I and III unload crudes into tanks directly and later may be blended from tank to tank to prepare the final crude feed. However, integration of scheduling and tank inventory, and composition modules, as discussed earlier in this blog, will be necessary to implement any blending schemes. Such integration of application modules would alleviate some of the physical and operational constraints.
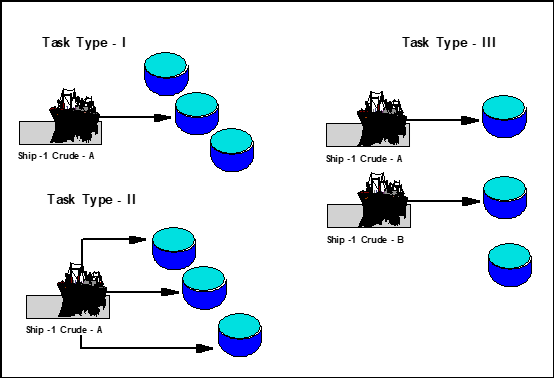
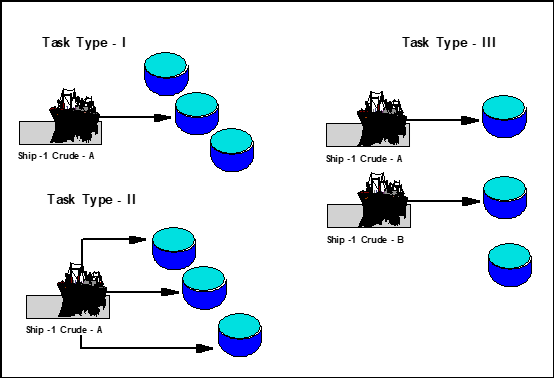
Figure 4. Configuration of “Ship to Tank” Transfer Activities
At any given time both physical and operational constraints govern the feasibility of one blending scheme over another. For example, physical constraints such as the availability of crude tanks will determine the feasibility of crude unloading and its blending into tanks at the same time or later for tank-to-tank blending configuration. On the other hand, operational constraints will determine the need for inline blending to crude units.
It is important to realize that although the integration of all modules discussed earlier in this paper would stabilize the quality of feed to distillation unit to achieve the product quality targets and improve the operational stability of the distillation unit, there may be a situation where an individual module is implemented for one reason or other. For example, if physical constraints do not permit for “ship to tank” or “tank to tank” blending of crude oil, inline crude blending to a crude unit can accomplish the same objective to a certain extent.
It is worth noting here that tank-to-tank blending has more degrees of freedom (depending upon the number of available crude storage tanks) than inline blending to crude units. In an inline blending scheme, crudes are blended usually for density control purposes only since the API density determines the crude distillation curve.
Products blending
The blending of products such as gasoline, diesel, and fuel oils has become increasingly complex process and demanding because of competition and new EPA regulations for the newly formulated types of gasoline. Refineries suffer big economic losses due to quality giveaways of Octane and RVP, time lost in reblending, not meeting markets demands because of inadequate product inventory due to shortage of tanks, etc. The refining industry around the world is placing emphasis on automation of their refining and blending operations using the latest technology to meet the market demands of tomorrow and stay in today’s cutthroat business.
This blog discusses the essential elements of an integrated blend control system for the planning, control, and optimization of their blending operations. This blog also presents the system architecture of an integrated blend control system using state-of-the-art equation solvers and optimization tools, blend models, software, and hardware sets. The blog also discusses the tangible and intangible economic benefits of an integrated blend control system.
Automation levels of blending control
In earlier years, before the advent of computers and digital instrumentation, refiners and others plants used to perform blending totally in a manual manner or “bucket mixing” approach according to predetermined proportions of ingredients. Severe competition, a decline in profits, and scarcity of raw materials forced refiners to consider other methods to stay in business. Three levels of blending control strategy have evolved over the last 15 years in the refining business and they are discussed briefly in the following paragraphs.
Regulatory blend control (RBC)
The first level of blend control strategy resides in a DCS such as ABB MOD-300, Honeywell TDC-3000, Fisher ProVox, etc., and controls the amount of each component in the final product tank automatically by computer. Although this level of computer does not give any guarantees to blend the product to specifications as it does not use any analyzer feedback, it does relieve the operator from monitoring the process continuously.
Advanced blend control (ABC)
The second level of the blend control strategy is a scheme that is implemented in another computer such as VAX, HP Workstation, IBM, etc., and is linked to DCS executing the first level of control. This control uses the analyzers feedback, corrects the recipe frequently, and guarantees the final product on specifications. This is a very complex technology and saves the refinery lots of money because of continuous optimization and feedback.
Off-line optimization and planning system (OOPS)
The third level of the blend control strategy is offline optimization of a blend recipe taking into account the refining process as expected in advance. This is done on a Personal Computer (PC) by a refinery planner and then he downloads the optimized recipe to the online blend control (ABC) system for further online control and optimization and is finally executed in DCS by RBC. The planner typically may plan many recipes at one time depending upon refinery operational characteristics.
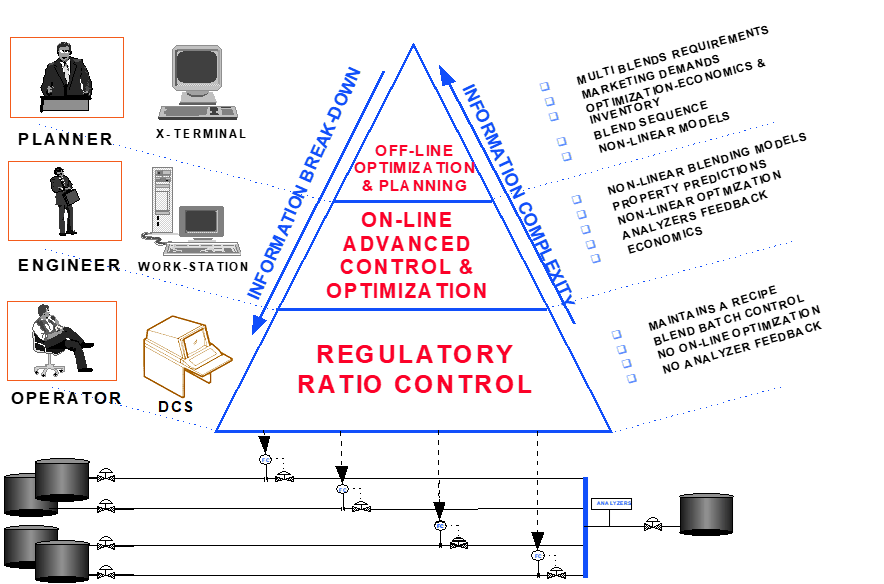
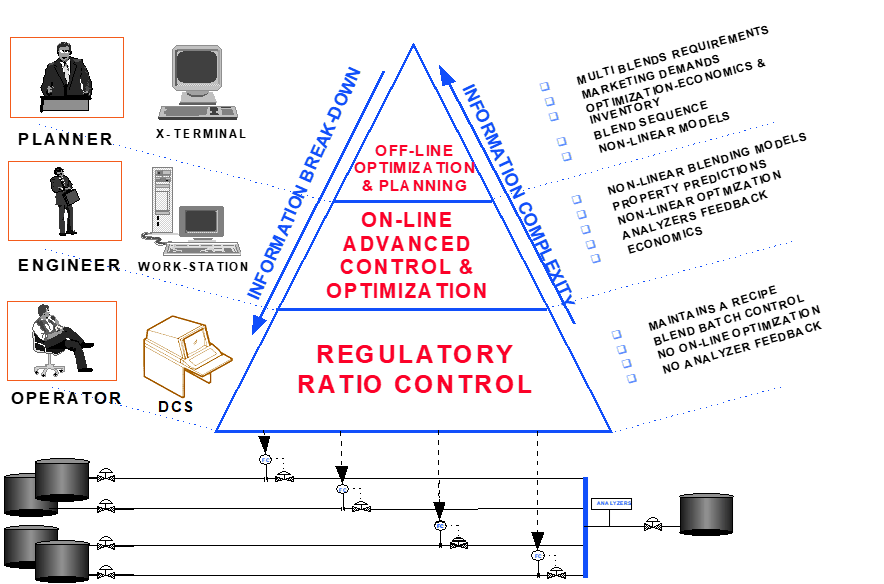
Figure 5. shows all levels of blend control, optimization, and planning system modules in an integrated environment
The integrated products blending system
Integrated blend control, optimization, and planning systems are implemented separately for the blending of middle-distillate and motor gasoline products in a refinery. Such an integrated system usually consists of the following minimum numbers of modules and is integrated through a Relation Database Manager System (RDBMS) such as Oracle, Interbase, Informix, Sybase, etc.
- Regulatory Blend Control System (RBC)
- Online Blend Control and Optimization System (ABC)
- Offline Optimization, Planning and Scheduling System (OOPS)
- Tanks Inventory Information System (TIMS)
- Tank Quality Information and Management System TQIMS).
- Online Blend History and Diagnostic Analysis.
- Blend Performance Analysis and Model Regression.
- Blends Information and Management System.
Figure -6 gives a typical architecture of an integrated blend control, optimization, and planning system. The modules in Figure -3 represent the minimum requirement for an integrated system. Although there are some other modules desirable in a more flexible and robust system, they will not be discussed in this blog.
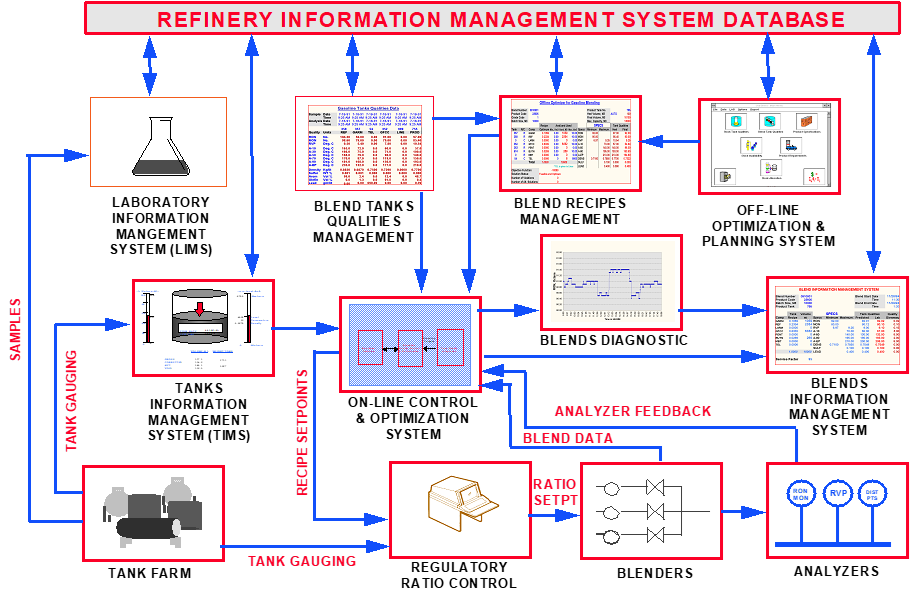
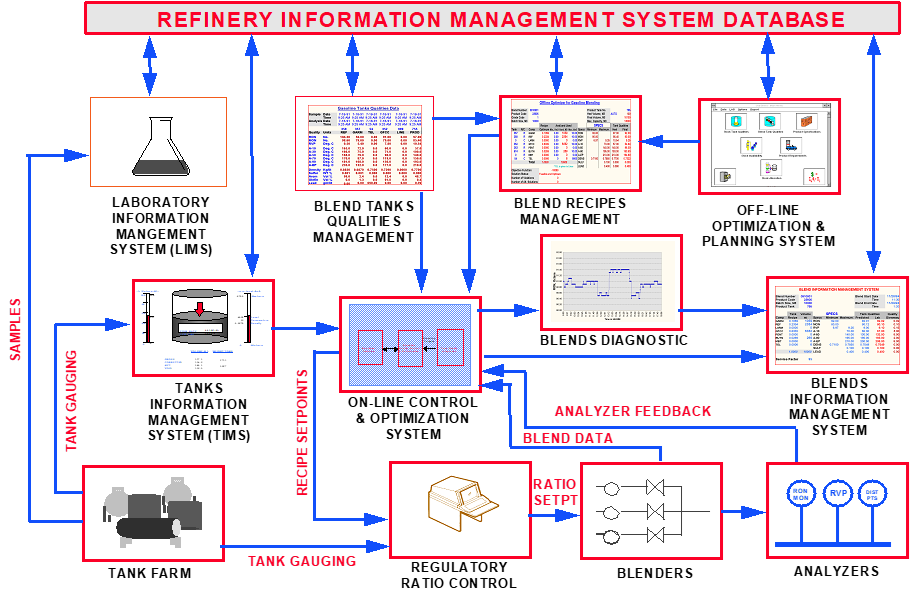
Figure 6. The architecture of an Integrated Blend Control, Optimization, and Planning System
Oil movement & storage
The functional capabilities of an Oil Movement and Storage (OM&S) system is primarily concerned with the transfers of bulk liquids within and across the refinery’s boundaries. Unlike the long-term, continuous, steady-state, and complex operating characteristics of the processing units, these bulk movements tend to be batch operations of comparatively short duration, imposing relatively simple control requirements. However, what makes the transfer activities tedious, performed manually, in a refinery is not the nature of their control functionality but factors like their numerous types, the large number of repetitions subject to inefficiencies, operating problems, and economic loss, etc.
This blog gives an overview of the typical refinery oil movement activities, problems connected with them, and concepts of automation of an Oil Movement and Storage (OM&S) system.
Refinery OM&S activities and their interactions
Typically, an oil movement and storage operation in a refinery involves efficient management of
- 100-300 Tanks
- 100+ Pumps
- 100-200 Remote Operated Valves (ROVs)
- 50+ Mixers
- 100+ Flow Temperatures and Pressure inputs
- 2000+ Manual valves
This equipment and tanks may be involved in one or more of the following activities:
- Receipts of Raw Material and/or shipment of Products using marine/truck/Rail cars/Barges/Pipeline
- Tank-to-Tank Transfer
- Process unit feeds and rundowns
- Custody Transfer/Meter Proving
- Product Batch/Inline Blending
- Recirculations
- Seasonal Storage of Materials
- Water Drainage
There may be as many as 80-90 different types of jobs or tasks involving these activities per day and these activities not only require the constant attention of the OM&S operator for the management of these tasks but they are highly interactive in nature, making them subjected to possible product contamination and accidents.
Problem areas of OM&S activities
It is quite natural that the management of such a large and complex network of equipment and transfer activities in a refinery and has some problems associated with it. Problems typically associated with OM&S activities can be classified into the following four areas:
- Decrease in Plant Profitability
- Operating Losses
- Product Losses
- Operating Costs
The following sections will discuss each of the above problem areas in detail.
Decrease in plant profitability
The plant profitability may be decreased due to the following factors:
- Product quality and/or quantity giveaway – Encountered in activities like blending and custody transfer due to lack of inline blending and accurate measurements.
- Product degradation due to displacement of previous line material – This happens if the same pipeline segment is used to transfer products of different qualities in activities such as tank to tank transfer, tank to ship transfer, etc. Product degradation usually requires either selling the product at a lower price or quality correction by reblending or the addition of corrective components.
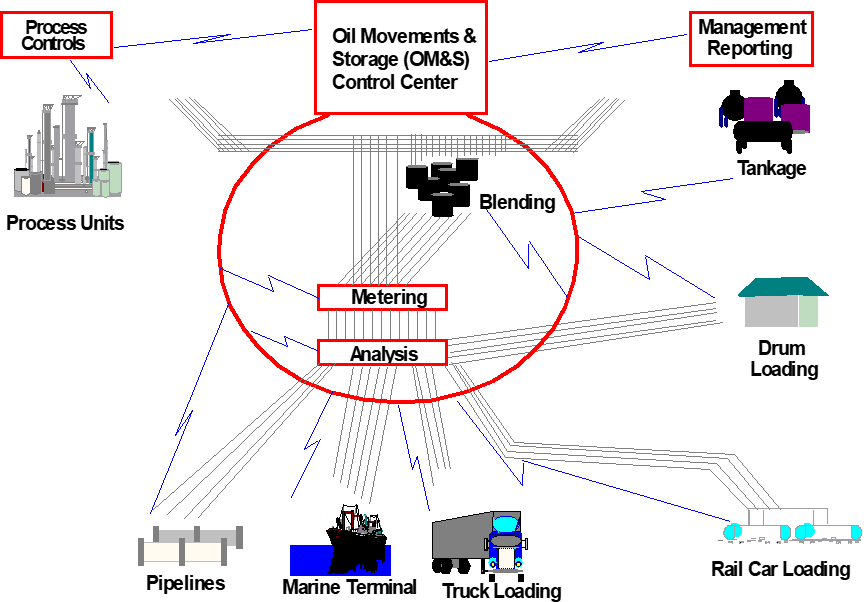
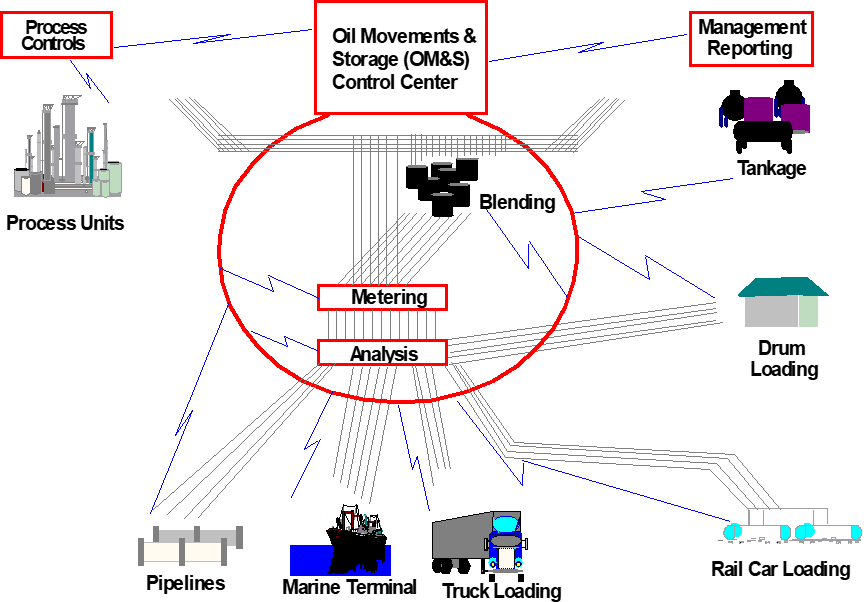
Figure 7. Interaction of OM&S Activities
Operating problems
Operating problems vary from the areas related to man/machine interfaces to errors by the filed operators and may result in economic losses. Some of the most common operating problems are:
- Multiple Operator Interfaces – It is one of the major concerns of the OM&Soperations in a refinery as the operator has to work with as many as 7-8 different types of displays and systems such as tank gauging system, DCS workstations, blend control, MIS computer, Laboratory Information system and at times reduces his /her effectiveness and results into operational errors which may be at times very expensive for the refinery’s profitability.
- Lineup Errors – The refinery has a very complex network of pipelines and field equipment. To line up various valves, pumps, etc., for a transfer activity requires careful execution and may result in product contamination if any errors are made in the lineup. Lineup activity by itself is also time-consuming and requires the availability of field operators in a timely fashion.
- Product Contamination – This may be a result of either lineup errors or due to unplanned or unauthorized movements.
- Pump cavitation – This situation could occur if the valve before the pump is stuck or does not open fully. Failure of the valve downstream of the pump could also damage the pump.
- Floating Roof Sinking -This problem may occur if the liquid in the tank may fall below a certain level due to a lack of timely action by the operator due to the failure of a low-level alarm.
Product losses
The direct effect of product losses is the decrease in the plant profitability and the followings factors contribute to this problem area:
- Inadequate and/or Erroneous Measurements – OM&S activities involving movement of products across the refinery boundaries such as custody transfer, marine loading/ unloading may incur product losses just due to inadequate or errors in measurements.
- Unplanned and unauthorized movements – This is related to human error either by the operator and /or field operators. The product loss may occur either in terms of the need to reprocess the contaminated products or sell at a lower price due to their downgraded quality.
- Leaks – Products leaks from valves and tanks result not only in product losses but also in present environmental hazards.
- Spills – Unattended tank during its filling or failure of high-level alarm may cause spills and thereby product losses and environmental hazards and clean-up cost associated with it.
Operating costs
In addition to economic loss to the plant by problems areas discussed in earlier sections, a plant may also incur an increase in operating cost due to the following factors:
- Large Plant Inventory – In the absence of any online and timely information and availability of raw material and finished products, the plant resorts to having a large plant inventory. Storage cost, unnecessary movement of products, not being able to respond to all market demands and fluctuation are some of the factors attributing to increased operating cost.
- Under-utilized tank Capacities – OM&S operators at times tend to fill tanks at levels lower than their maximum due to fear of tank spills and failure of alarm. This results in underutilization of tank capacities and increases in operating cost as enough raw material and/or product may not be available for manufacturing or shipment.
- Wasted Energy – Electric utilities cost increase as the transfers are either repeated due to human error or execution of avoidable transfer activities.
- Demurrage Charges – This is quite a substantial loss to the refinery in terms of demurrage charges payable to shipping companies due to delays in marine loading and unloading and ships have to wait at port longer than necessary.
- Large Man-power – Manual operations of opening and closing of valves, pump start / stop sequences require a large number of field operators for the transfer activities. In addition to that, more maintenance personnel are also needed to maintain the field equipment to repair them in time.
- Improper and untimely Reports – Lack of any automation and/or implementation of an information system may not provide inventory reports in a timely and accurate fashion for day to day planning cycle of the refinery operation.
Most of the problems in the areas discussed in the above sections can be either eliminated or reduced by implementing computer automation of oil movement and storage. The next sections will discuss some of the concepts and features of the automation of OM&S available today in the market.
Computer automation of OM&S
The automation of oil movement and storage operation requires that the computer system responds to the needs of the operator to perform the major functions discussed below.
Functionality
- Utilize remote readings from tank gauges to:
- Calculate inventories, conditional events, total volumes shipped.
- Monitor tanks for improper movements, alarm on high, low levels.
- Respond to field element status:
- Monitor remotely operated valves (ROV’s), pumps, and mixers for alarm conditions and proper response operator requests.
- Keep a list of out-of-service equipment.
- Provide status information to an operator
- Monitor and control movements for receipts, rundowns, transfers, and shipments.
- Select equipment (tanks, valves, pumps, etc.) for moves required in the schedule.
- Automatically sequence equipment to implement and terminate moves.
- Terminate movements, swing tanks, start other movements, etc. when specified conditions are met.
- Provide interfaces between DCS and supervisory level controls of in-line blenders and equipment sequencing, movement monitoring, and customer blend control strategy programs.
- Provide summary reports, movement logs, and profiles that are defined by the customer.
- Utilize shared disks to support the computer to receive operating data and transmit historical data.
The above characteristics of a well-designed and developed OM&S computer system provide interfaces and interaction among all activities of OM&S operations in a refinery. Figure -8 shows the flow of information among OM&S activities and OM&S computer system,
Levels of OM&S control functions
The functionality of automated OM&S system can be translated into various control levels, as shown in Figure -9., are discussed below:
- Level-0 – This is the lowest level at which all field equipment such as pump, ROV, mixer, and control valve are controlled by the electronic system. Tank levels and temperature are also monitored at this level.
- Level-1 – This level is called supervisor control where a computer system either monitors the status of process variables, field equipment status and sends the command for the remote control operation. For example, instead of starting or stopping a pump from the field or remote panel, the operator could issue a command from the computer to operate a valve or pump. Tank gauging systems such as Wessoe and Varec provide computer interfaces to monitor tank levels and temperatures.
- Level-2 – This level involves extensive application programming and offers the maximum benefits of automation. Various steps of executing an OM&S activity are automated at these levels and categorized into separate modules such as task definition, sequence generator, and control, task monitor, etc. Blending is also implemented at this level.
- Level-3 -This is the topmost level and is usually termed as information system level. Information about various refinery activities such as planning, scheduling, shipping, and dispatching is collected at this level and interfaced with OM&S control modules for the overall integration of the system.
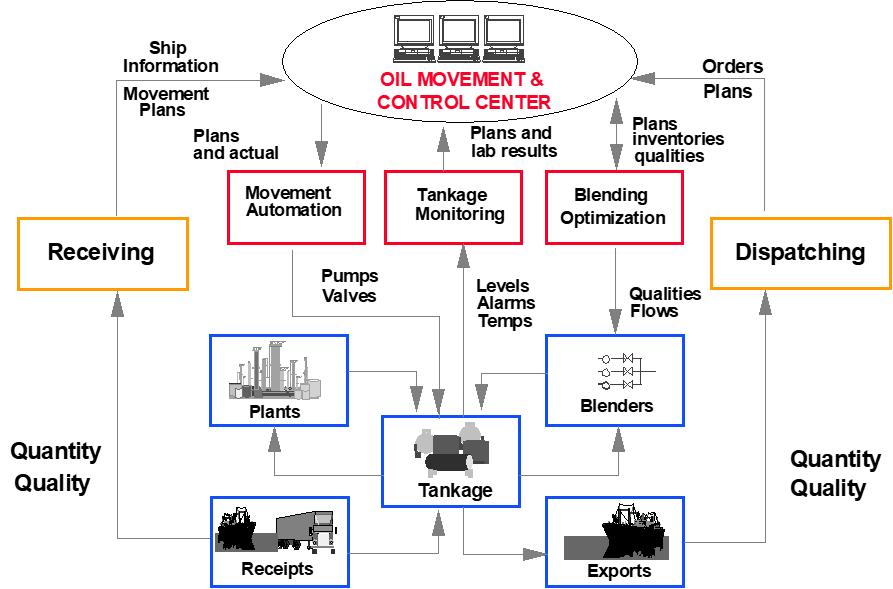
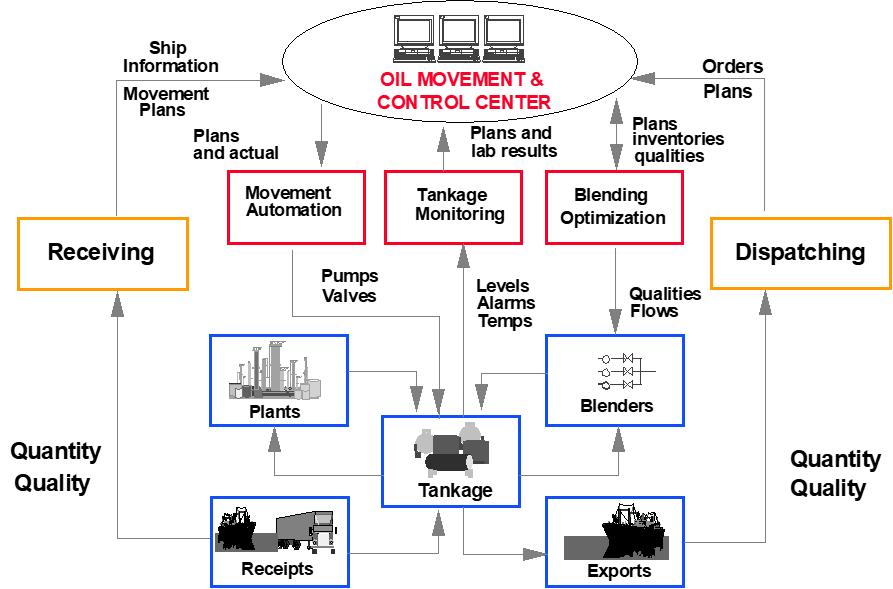
Figure 8. Computer Automated OM&S System
System integration
The components of an integrated OM&S computer system would depend upon the status of automation and refinery information systems in a particular refinery and the computing platforms of the OM&S system. For example, commercially available OM&S systems either from IBM or Honeywell include blending as one of the modules. OM&S algorithm as such does not include any linear programming (LP) algorithm whereas the inline blending uses either LP and non-linear equation solver and optimization using non-linear blend models depending upon the type of product blend. In addition to this, a truly integrated OM&S system must interface with the refinery’s information management system for history, databases, reports, reconciliation, etc. This results in customized integration of the OM&S system for each refinery and may involve developing many interfaces for various modules and computers.
Figure -10 shows a typical automation architecture of an OM&S system.
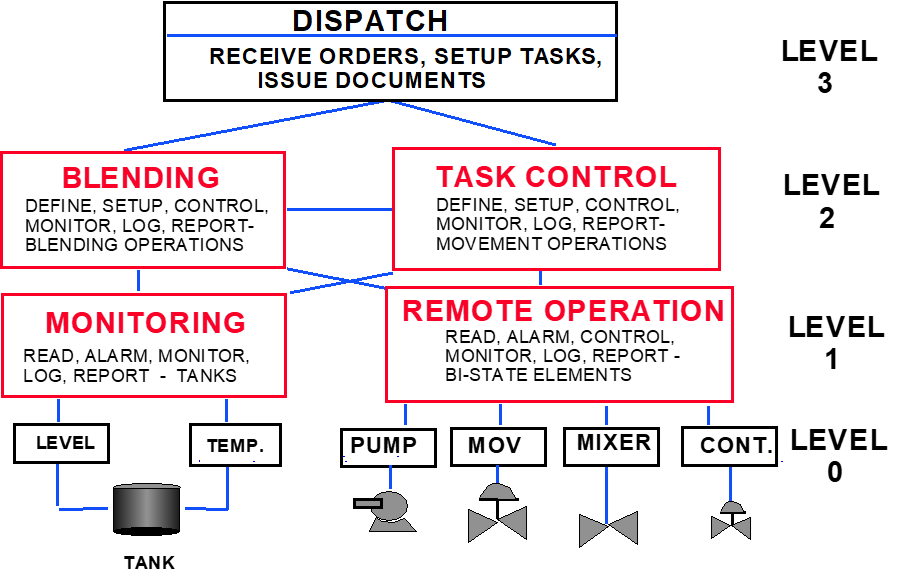
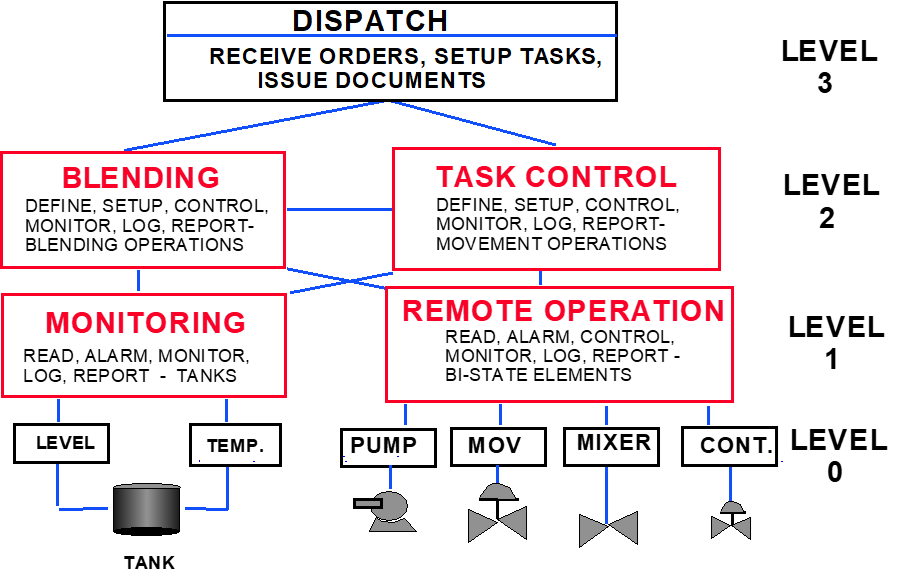
Figure 9. Control Levels of Automated OM&S System
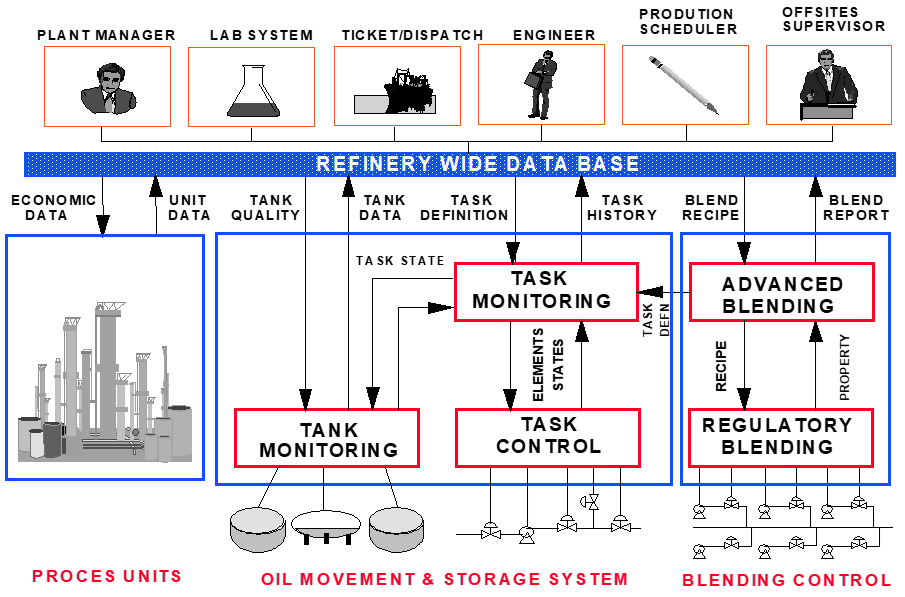
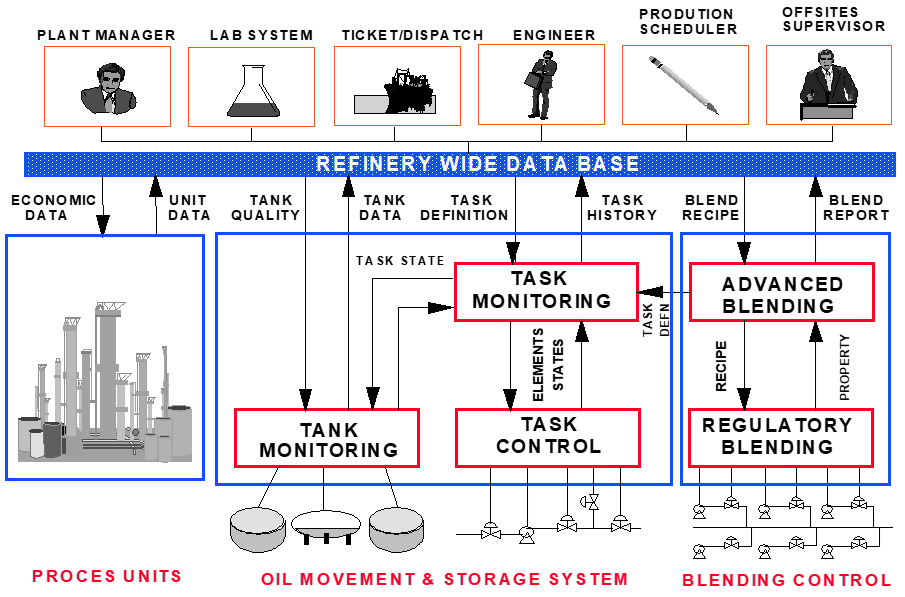
Figure 10. The architecture of a Typical Integrated OM&S System
Benefits
An integrated blend control and optimization system offers great economic benefits for a typical refinery and various modules discussed in this paper offer both tangible and intangible benefits. Table-2 shown below summarizes a typical range of average benefits for a 100,000 Bls/day refinery. The typical payback period for the implementation of an integrated blending system is usually 1-2 years.
Table 2 Tangible Benefits of Integrated Advanced Control Systems
Integrated System | Potential Benefits ($M/Year) |
Crude Blending Control and Optimization System | 2-3 |
Products Blending, Control & planning System | 5-7 |
Oil Movement & Storage System | 3-4 |
Total=$10-14M/Year
Summary
This blog has discussed the concepts of three major integrated control systems which can save a refinery between 10-14 M$/Year in benefits. However, these systems can be implemented in phases to realize each one of them individually. Since oil movement and storage system is used for both blending systems, it must be implemented first keeping in mind the overall integration of all three and other computer systems in the plant.
References
- Advanced Process Control handbook IV, Hydrocarbon Processing, March 1989.
- Agrawal, S.S., “Computer Integrated Manufacturing (CIM) for Process Industries -A Perspective”, presented at BIG’ 90 conference, Pune, India, May 23-25, 1990.
- Agrawal, S.S., “Economic Benefits of An Integrated Oil Movement & Storage (OM&S) Storage System”, Manuscript sent for publication/presentation
- Agrawal, S.S., “Functional Requirements for Integrating MIS with Advanced Controls”, Presented at the Sixth Annual Control Engineering Conference, Chicago, Illinois, U.S.A., May 19-21, 1987.
- Agrawal, S.S., “Modular Integration of An Advanced Blending, Control, Optimization an Planning System”, Manuscript sent for publication/presentation
- Agrawal, S.S., “Modular Requirements to Integrate MIS with Computer Control Systems”, Presented at ISA International Conference and Exhibit, Anaheim, California, U.S.A., October 4-8, 1987.
- Agrawal, S.S., “PC Based Distributed Supervisory Control for Process Industries”, presented at ISA Bombay Chapter conference, Bombay, India, May 5-6, 1991.
- Agrawal, S.S., “Scope and Feasibility of Integrated Crude Blending Control and Optimization System”, presented at ISA ‘94 Philadelphia conference, U.S.A, May 5-6,1994
- Agrawal, S.S., “Scope of An Integrated Oil Movement & Storage (OM&S) Storage System”, Manuscript sent for publication/presentation
- Bain, M.L., Mansfield, K.W., Maphet, J.G. et. al, “Gasoline Blending with an Integrated On-line Optimization, Scheduling and Control System”, Paper no. CC-93-131, NPRA Computer Conference, New Orleans, Nov. 17-17, 1993
- Brooks, Robin, “Experiences with Oil Movements and Storage (OM&S) systems within Integrated Refinery Management Systems”, CC-93-128, Proceedings of NPRA Computer Conference, New Orleans, November 1993.
- Czech, Robert S., “The Application of Computer Systems in Refinery Oil Movement Operations”, Proceedings of ISA Conference, Philadelphia, May 1983.
#IntegratedRdbmsModule #IntegratedRdbmsModule #ProductsBlendingControl #CrudeQualityControlIntegration #On-LineBlendControl #RegulatoryBlendControl #PhysicalRefineryConstraints #ConfigurationsBlendingSchemes #RefineryCrudeBlending #OilMovementStorage #RefineryFeedStocks #OperationalDataAnalysis #Off-LineBlendControl
1 2 3 4 5 100%
1 2 3 4 5 0%
1 2 3 4 5 0%
1 2 3 4 5 0%
1 2 3 4 5 0%