Introduction
It is absolutely necessary for a refinery to recognize required “enterprise Changes” and an efficient and cost-effective system design to upgrade the existing blending system to an advanced blending control system. Part-I of this series discussed the changes required in “enterprise culture” to undertake an upgrade project and be able to sustain its expected ROI consistently in the future. Part-II of this series addresses the second component of this upgrade project, namely, what are hardware and software required and how to design and select an efficient and cost-effective advanced blend control System?
Almost all refinery management desires to install a world-class advanced blending control system and hurries to install the best of the best in each category, for example, analyzers, DCS, advanced control software from various vendors and assume they got the best system in the world. The problem is that in this process, they end up installing expensive components with low ROI and ignores relatively simple yet efficient components to give them a bigger and longer ROI. This paper identifies and discusses design considerations of all hardware, software, interface components of an advanced gasoline blending control system, their relative cost-benefits analysis, overall system integration, and strategy for phased system commissioning. The paper also presents methods to benchmark the presently existing system using industry practices to arrive at an estimate of the investment required for the upgrade project.
Plant survey
The management of a mid-size refinery had contacted Offsite Management Systems LLC (OMS) to conduct a preliminary one-day plant survey to ascertain if their current regulatory in-line Gasoline Blending Control system can be justified economically to upgrade to an advanced blend control system per the current refining industry practices. OMS conducted the survey to determine the existing state of eight (8) areas of gasoline blending, shown in Figure-1, and interviewed management, planner, blending engineers and operators, analyzer and lab technicians, and walked through the entire process from enterprise-wide planning to final blend execution and reconciliation. OMS concluded that all areas of the refinery’s gasoline blending control system were sub-optimal and below the average of industry standards. It had the potential of saving of 6-8 MU$/year by upgrading the system to an advanced blending control system and required an extensive Master Plan Study to evaluate and design the architecture of the blending system to capture the speculated benefits.
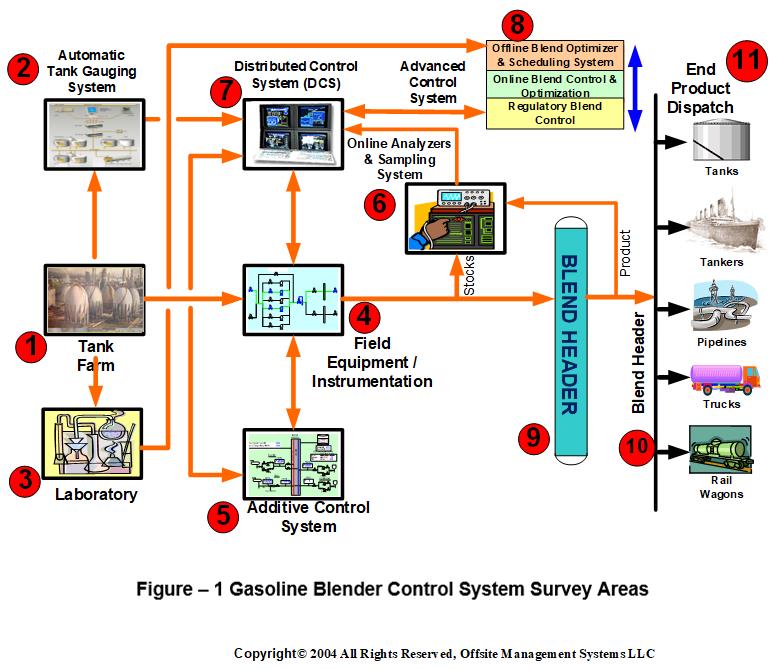
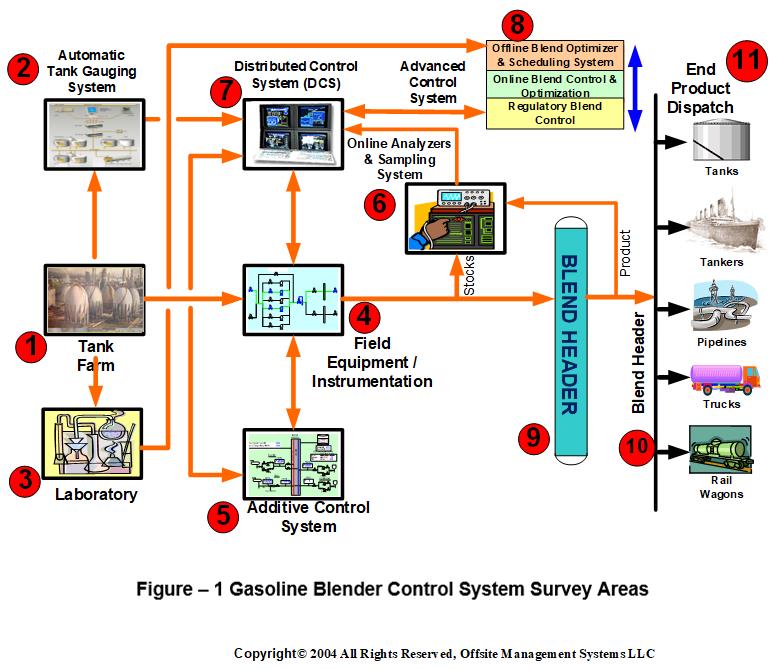
Figure 1. Gasoline Blender Control System Survey Areas
A few months later, the refinery management contacted Navigator Consulting and Offsite Management Systems to conduct a detailed Master Plan Study to assess the organization’s capability and also prepare a blueprint for the architecture of a Gasoline Advanced Blending Control System. In an earlier blog, authors had discussed the organizational capability required for the upgrade and this paper will discuss all the technical aspects of the advanced Gasoline Blending Control System.
Blending configurations
It is a myth in the refining industry that to capture all tangible benefits from a Blending Control System, one must invest in the best of the best hardware and software and then management waits for years for the approval of capital funds for the blending project. The truth of the matter is that the bulk of benefits comes from low expensive components and improved operation strategy. In this paper, we will discuss these factors as documented in the actual study. Refineries adopt a variety of blending configurations for one reason or another and it affects significantly how a blending control system can be designed, configured, and implemented. The following paragraphs discuss various blending configurations and their impact on the blending system design.
Modes of Blending – Blending operations can be either to blend directly from process units usually referred to as “run-down blending” normally for Diesel and kero products or to blend from tanks to tanks for gasoline products and crude oil. Some refineries also have tank-to-tank blending for Diesel products.
Types of Blending – Tank-to-tank blending can be either sequential, that is one tank at a time or in an inline blending where all components are blended simultaneously into one product tank. Although sequential blending is the least automated and loses most of the tangible benefits, it can still capture some of the tangible benefits by implementing strategic software like offline blend optimizer and tanks quality tracking system as discussed later in this blog.
Source of Blend Stocks – In the refining industry, blending stocks originates from a variety of sources such as stock tanks, process streams direct to header or process streams pooled to tank and then to header. Each of these sources affects the choice of hardware and software components for the blending control system. It is best recommended to avoid the use of direct streams to headers and should be pooled to a tank for a better control strategy. Additionally, refineries with a minimum of two tanks for each stock type and using them in closed mode, that is no input stream coming in while blending, can realize the optimum blending operation with maximum realized benefits.
Blend Headers Interactions – Although multiple products blending by using multiple headers is a common operation for run-down blending for Diesel and Kero products, they are also used for blending simultaneously leaded and unleaded gasoline products in some countries. This requires a robust and comprehensive blending control system as there can be no contamination and the same stream is shared for more than one blend header.
Product Destination – The product can be blended into a tank and then shipped out later or it can be blending directly to pipeline or ship. For pipeline or ship blending, the online blend control software and online analyzer must be proven and robust for online certification as there is no chance for reblending contrary to the case of blending to a tank.
Dedicated Control Loops – It is highly recommended that there should be one dedicated control loop for each blendstock. The refinery in this study had more stock circuits than control loops and has an inefficient and time-consuming operation to line up control loops for stocks and loses blending flexibility and tangible benefits. The stocks should also be categorized carefully to differentiate them with respect to cost and qualities to better control and optimize the blend for maximum profitability.
Field equipment
A typical example of automation of blending field equipment is shown in Figure-2 and they cover tank gauging systems, pumps, limit switches, motor-operated valves (MOV), and recirculation valves. With the exception of the Automatic Tank gauging system, automation of other elements does not significantly add to the tangible benefits. However, they may be desirable for the automatic lineup, minimization of human errors, safety, and fully automated blending operations points of view. Typically, the benefits from the automation of field equipment are 10-15% with 30-40% of the total project cost. It is advisable to revamp the field equipment automation only while upgrading from total manual to fully automated advanced blending control system but may not produce justifiable ROI for an existing inline blender with partial automation of field equipment as concluded in the present study.
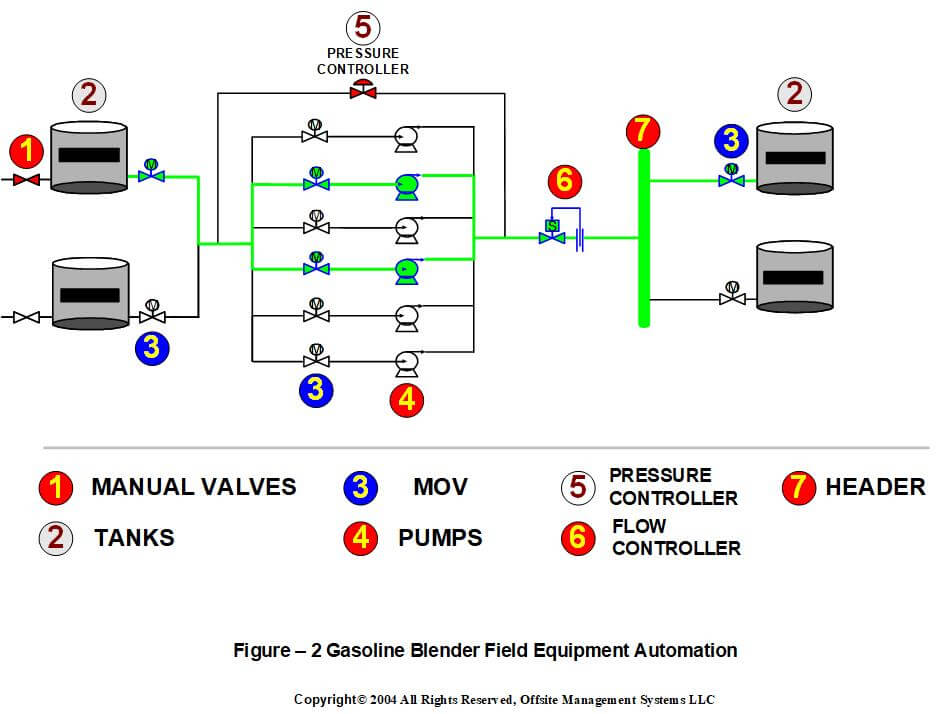
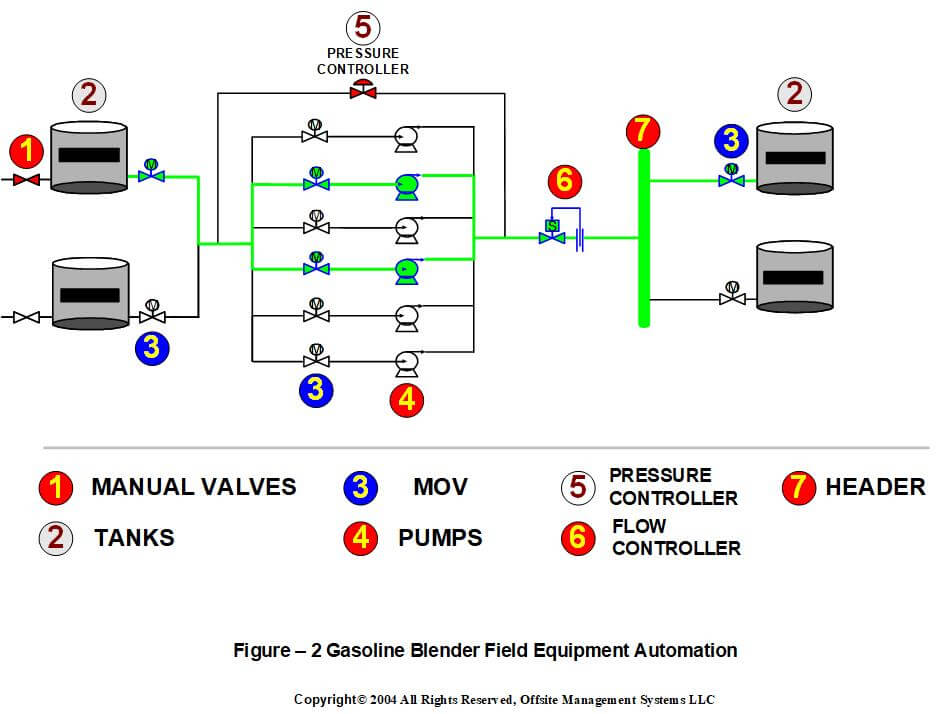
Figure 2. A Typical Example of Automation of Blending Field Equipment
Automatic Tanks Gauging system (ATG) is required to monitor tank inventory for offline/online blend control and optimization, custody transfer purposes, inventory tracking, and refinery planning. It should be configured for all required signals such as level, temperature, density, pressure, and water level to serve suitably to all refinery business and control applications.
Analyzers and sampling system
Online analyzers such as CFR octane engines or multi-analysis Near Infra-Red (NIR) are deployed to analyze the qualities of blend components and/or product header and depend strongly on the blending configuration as discussed above. For example, if the refinery has tank-to-tank, two tanks/component closed, no direct or wild stream type of configuration, online analyzers do not add any value to overall benefits. This is because the blend component qualities are static during blending and blend ratios would not change from initially optimized ones using lab analysis of blending tanks. But this is not a common blending configuration due to various processes and economic constraints. Figure-3 shows typical setups of online analyzers and lab analysis for gasoline blending using either CFR engines for product only or NIR analyzers for both components and products. The refinery in the study had only two sets each of RON and MON CFR engines (total of 4) for product headers only and stock qualities were analyzed by lab samples only.
The setup in Figure-3 or the one at the refinery in this study has severe deficiencies in terms of lack of in-time availability of lab analysis of stock tank qualities, lack of blend control for direct stream qualities, and no ability to adjust blend ratio to produce final blend on specs economically. This configuration results in about 10-15% reblends and quality giveaways. Refineries using the online NIR analyzers as in Figure – 3 have superior blending control and performance except for offline blend optimization. Refinery blend planner or blend optimizer engineer still has to depend on lab analysis of stock and final products tanks before they plan and optimize the next blend. This usually becomes a bottleneck for the blend production schedule as it sometimes takes 8-12 hours before all tank samples are analyzed and reported by the lab.
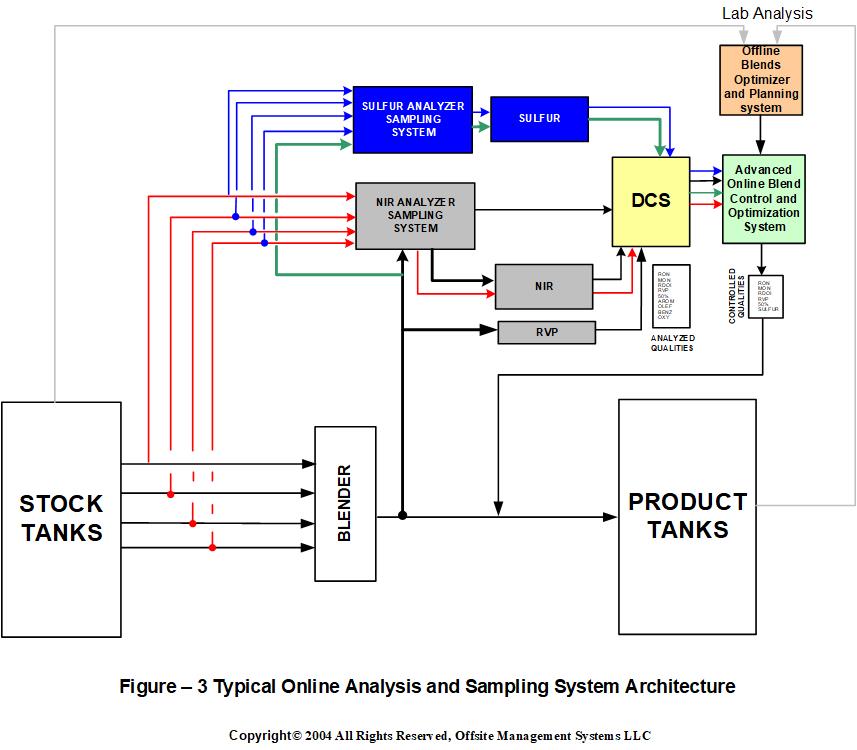
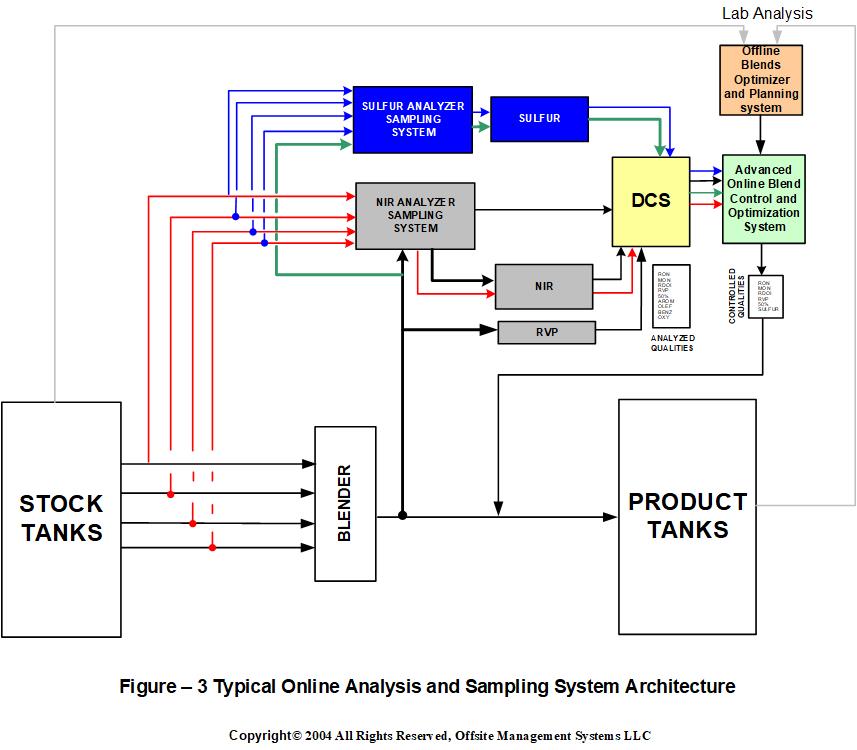
Figure 3. Typical Online Analysis and Sampling System Architecture
Figure-4 shows recent development in advanced blending control technology by Offsite Management System LLC to install a tank tracking system (gomsTQTS™) which uses the non-linear blending models to predict the qualities of all stock and products tanks in near real-time. This architecture removes all limitations of the in-time availability of stock qualities as mentioned above and offers additional features of upstream unit feedback control and optimization. Additionally, authors have estimated an average savings of about 1-1.5 MUS$/year in a decrease of lab sample and analysis load by the implementation of a tank quality tracking system as discussed in this paper. Details of this technology are outside of the scope of this blog and will be presented elsewhere or can be obtained by contacting Offsite Management Systems LLC.
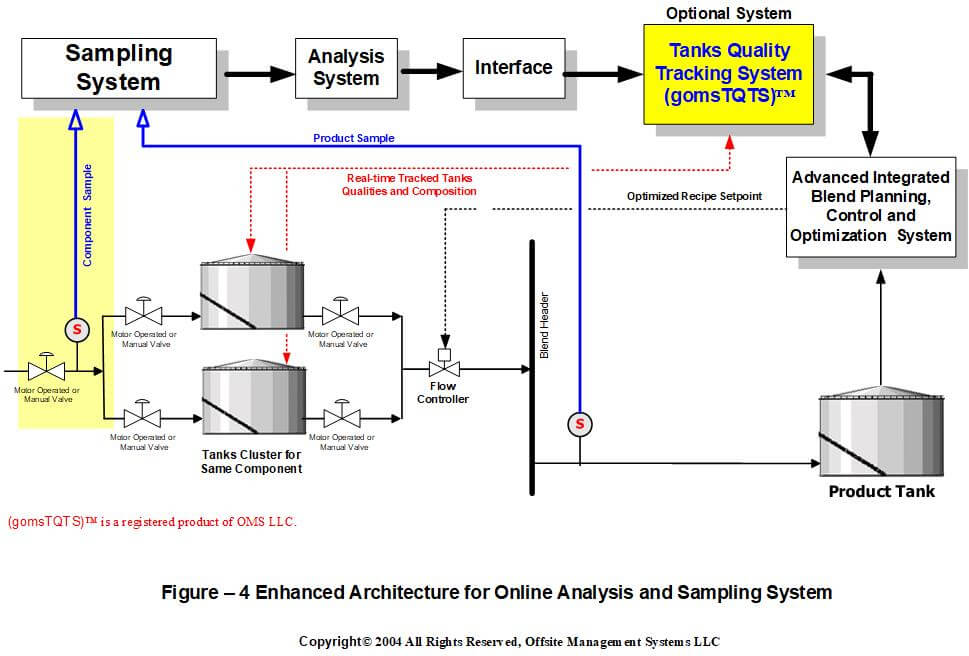
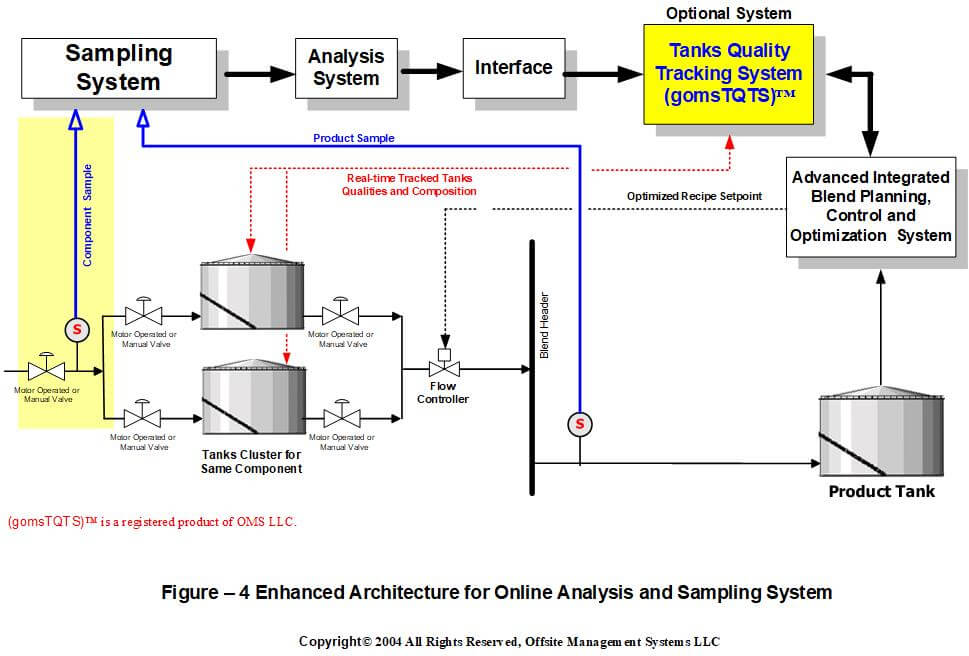
Figure 4. Enhanced Architecture for Online Analysis and Sampling System
Computer Hardware
A typical PC-based client-server architecture is used for the advanced blend control system and it is interfaced with DCS (Distributed Control System) or PLC-based system. As it will be discussed in the following paragraphs, the lowest blend regulatory control level is resident in DCS and it interfaces with all field equipment, online analyzers, controllers and tank gauging system, and ATG computer. It is recommended to implement advanced blend control system modules which are independent of the DCS platform and not strictly connected with DCS for ease of upgrade and to take advantage of the latest development in blend technology.
Software
Refinery Planning and Scheduling – Refinery planner uses LP-based tools to plan refinery supply, production, and dispatches schedules usually for a month’s duration, and downloads the information to different departments including blend engineer for the execution of plans. The refinery may update the plan during the execution progress if there exists a feedback and reconciliation mechanism in the refinery; otherwise, it is done at the month-end. This step also generates average blend recipes and blend product targets using average properties and production rates for the blend engineer to further optimize and execute.
Offline Blend Planning and Optimization – The blend engineer starts with the monthly plan given to him by the refinery planner as explained in the above step and optimizes each blend individually 18-24 hours before its execution and freezes its recipe for online execution. The blend engineer typically may plan many recipes at one time depending upon refinery operational characteristics. A number of tools are used for this step by different refineries and they include GRG2 optimizer solver in MS Excel, linear blend models, and linear LP optimizer or more robust non-linear blend models and non-linear optimizer. Offline blends optimization, if done correctly, achieves the maximum tangible benefits with or without the implementation of an online blend control. The benefits from this step are typically 40-45% of the total ROI with the non-capital investment of less than 5% of the total upgrade project cost. This benefit can be further increased by 10-15% with negligible additional investment by implementing another system for the online tank quality tracking as discussed below. One of the deficiencies is the lack of availability of current tank qualities for offline optimization and the blend engineer has to wait 18-24 hours for lab analysis of tank samples and can be minimized by the next module.
Online tanks Quality Tracking System – One of the problems any refinery faces is the availability of current tank qualities as the lab analysis of tank samples are available only in 12-18 hours or longer and the tank qualities may be already outdated in this duration. This leaves blend engineers with old qualities to optimize the blend recipes and may result in either an off-spec blend or one with a large-quality giveaway. This situation is not helped even by the installation of online analyzers as still don’t give the qualities of tanks when not blending. Offsite Management Systems has developed a technology and strategic placement of online sampling points to predict the tank’s qualities in near real-time. This system is estimated to save refinery in lab analysis load by more than 1-1.5 MUS$/year and has increased the overall benefits of blending control by 2-3 MUS$/year.
Regulatory Blend Control (RBC) – This is the first and mandatory level of blend control strategy and is also known as Blend Ratio control (BRC). It resides in a DCS (Distributed Control System) for systems upgraded from batch or manual to inline blending. For smaller size refinery (< 20-30KB/day) this level of control may be accomplished by implementing a PLC-based system to be cost-effective. This level controls the amount of each component in the final product tank automatically by a computer and potentially can increase the total product throughput by about 10-15% thus giving tangible benefits of about 5%. Although this level of computer does not give any guarantees to blend the product to specifications or economically optimum recipe as it does not use any analyzers feedback, it does relieve the operator from monitoring the process continuously. However, it is also very common even in larger-size refineries, without advanced blend control in place, to use this level for “trim” control where one component is designed to top-off one controlled quality in the final tank. For example, Butane is used for the trim control of RVP, and Alkylate or a similar component may be used for RON.
Online Blend control and Optimization – Online blend control and optimization is used to optimize blend ratios online for changes in component tanks qualities or for any direct streams to the blend header. This control level is necessary and beneficial only for such cases. Practically, if the blend configuration has two tanks for each component with a closed tank while blending, the qualities do not change during blending and ratios will remain the same for practical purposes. Another reason for this control level is to correct offline optimized blend ratios which may be based on old qualities. However, the implementation of an online tank quality tracking system as described earlier will eliminate this problem as a blend engineer can optimize the recipe very close to the blend execution schedule or the blend operator can revise the initial recipe. This control uses the analyzers feedback, corrects the recipe frequently, and guarantees the final product on specifications.
In addition to the above-described software systems, it is also beneficial to include blend reconciliation and model regression modules as shown in Figure-5.
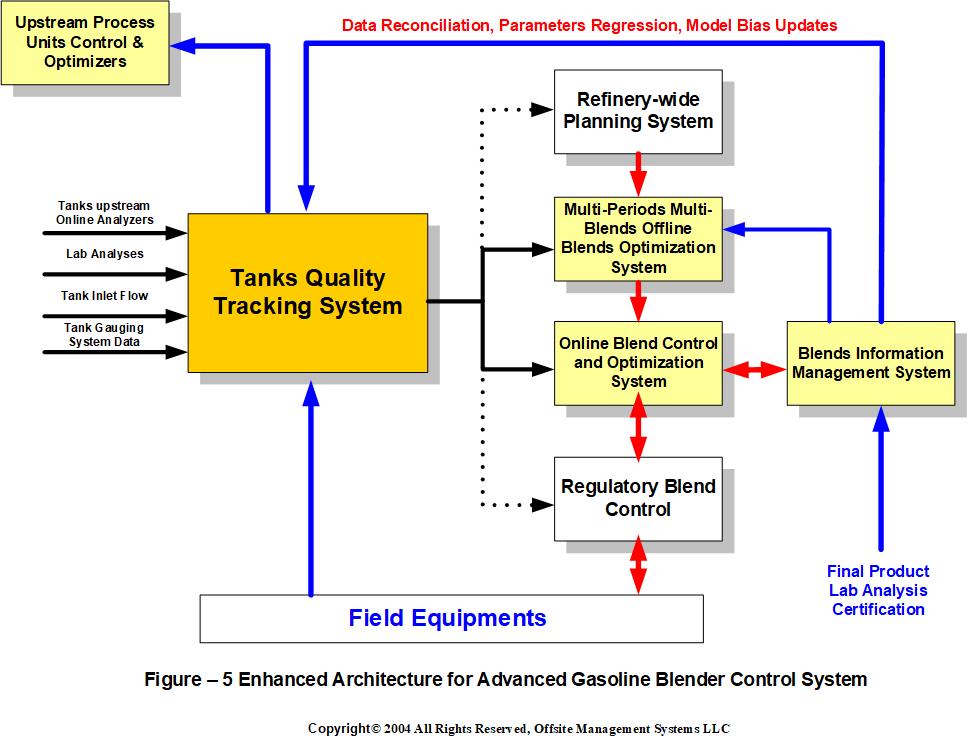
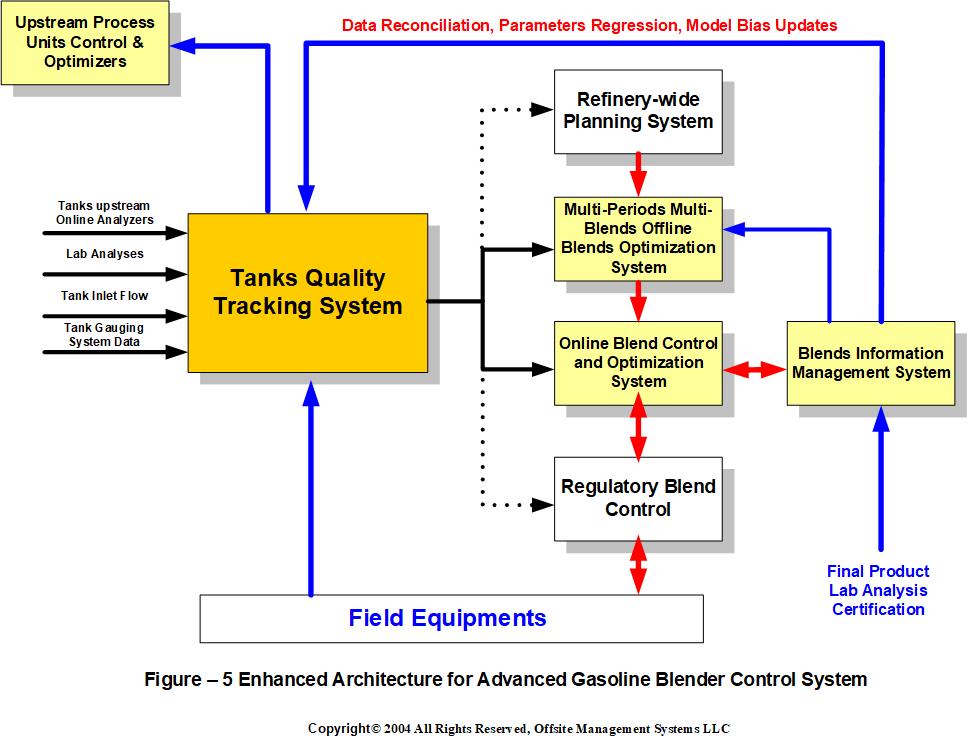
Figure 5. Enhanced Architecture for Advanced Gasoline Blender Control System
Cost, benefits, and implementation
Benchmarking – The refinery wanted to know where they stand in the industry with respect to their advanced gasoline blend control system. There is no objective methodology to answer this question. However, the closest we came to categorizing all areas and sub-areas of an advanced blend control system and assigning them a degree of importance, or weighting factor, in the overall system upgrade strategy. Then we reviewed each of these areas for the refinery and assigned it a % status level. A combination of this criterion and the refinery state generated a benchmark index for the refinery. This index is estimated to be accurate within ±10%. This index also indicated the level of investment (within ±15%) required to upgrade the existing gasoline blending facilities to an industry-standard advanced blend control and optimization system.
Cost and Benefits – It is interesting to note that 65-70% of tangible benefits from the upgrade of gasoline advanced blend control system are derived by investing only 10-15% of the total project cost within 3-6 months of project initiation and the rest of 30-35% benefits accrue over next 18 months by investing 80-85% of the cost. Additionally, initial benefits are immediately visible and they “pay as you go” while other benefits start only after completion. This simple fact is often taken lightly by refining management and they wait for the full capital project budget approval cycle and take 2-3 years for its materialization. It is easier to execute a gasoline blending upgrade project in phases as suggested in this paper for the immediate realization of benefits and pay for the later phases of the project. Figure -6 shows cost and ROI with reference to project phases over their execution duration.
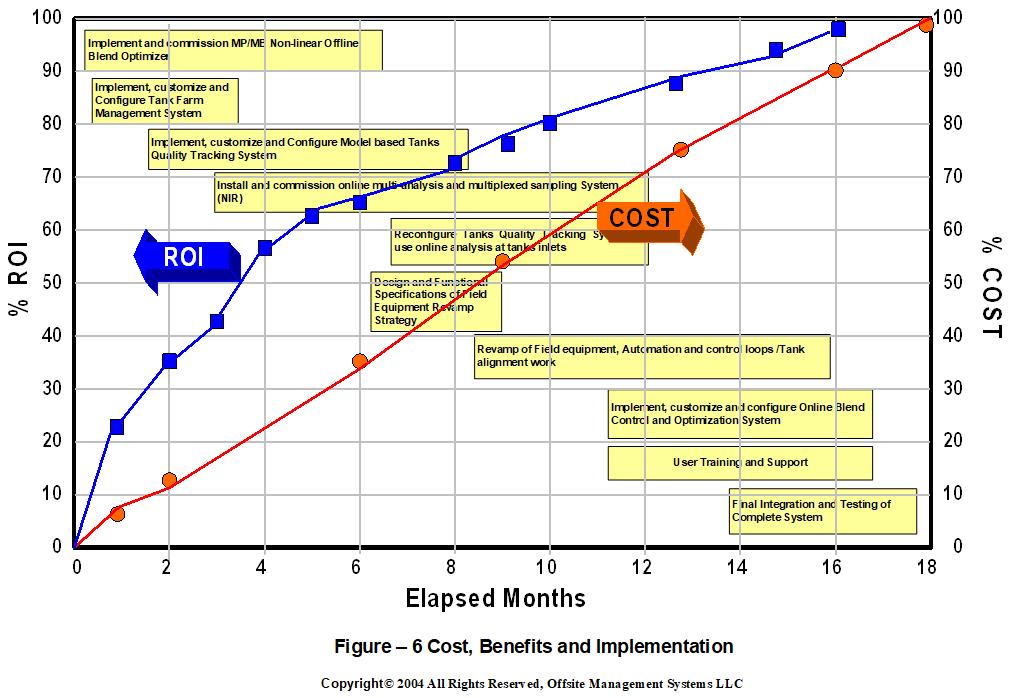
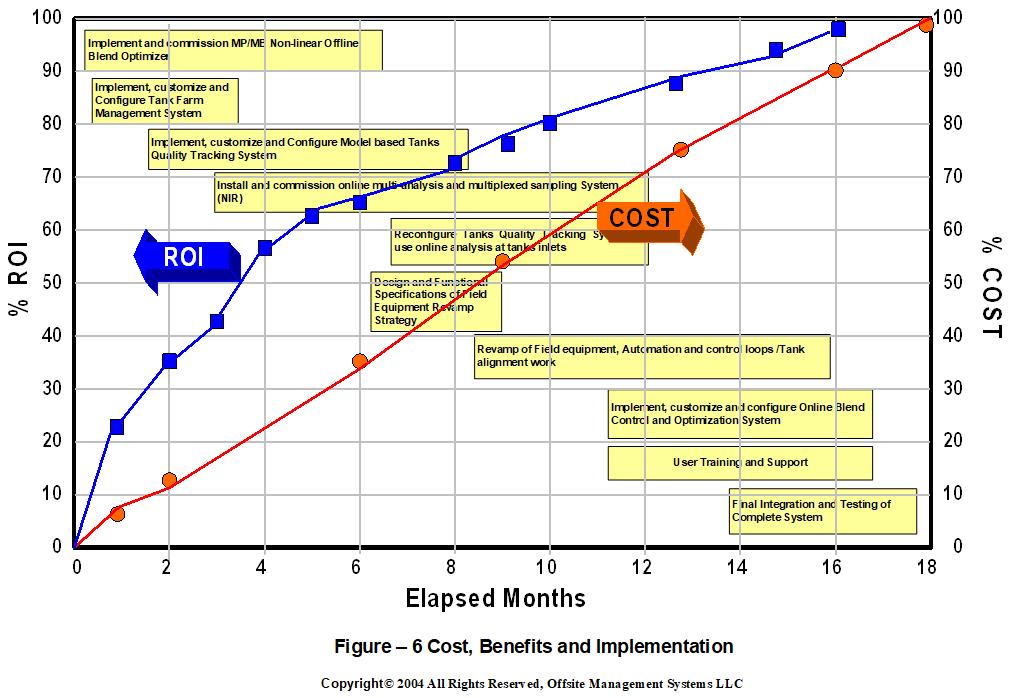
Figure 6. Cost, Benefits, and Implementation
Summary
This paper has presented all aspects of design consideration to upgrading gasoline blend control system in a refinery either from a totally manual operating system or a partial advanced control system to a complete and industry de facto advanced gasoline blend control system. The paper has suggested a recommended implementation strategy to realize most of the stipulated tangible benefits immediately after the project kick-off. The blog was a result of a case study of preparing a master plan, data analysis, and a detailed plant survey for a mid-sized North American refinery. Earlier part-I of this paper series discussed and presented the changes required in enterprises to effectively and successfully undertake an upgrade project for the advanced gasoline blend control system.
#AutomaticTanksGaugingSystem #Multi-AnalysisNearInfrared #LabRefineryAnalysis #MinimizeQualityGiveaways #RefineryFieldEquipment #AnalyzerSamplingSystem #Enterprise-WidePlanning #RefineryBlendingConfigurations #OffsiteManagementSystems #GasolineBlending
1 2 3 4 5 100%
1 2 3 4 5 0%
1 2 3 4 5 0%
1 2 3 4 5 0%
1 2 3 4 5 0%